Diese Bedienungsanleitung ist als Leitfaden für den Betrieb der RFlex Presse gedacht. Um eine optimale Leistung Ihres Schweißgeräts zu gewährleisten, befolgen Sie bitte die Empfehlungen und Spezifikationen genau.
Inhaltsübersicht
- Kapitel 1: Bestimmungsgemäße Verwendung
- Kapitel 2: Sicherheitsschilder und Piktogramme
- Kapitel 3: Technische Daten
- Kapitel 4: Technische Beschreibung
- Kapitel 5: Montage und Installation
- Kapitel 6: Betrieb
- Kapitel 7: Auswahl der Schweißparameter
- Kapitel 8: Wartung
- Kapitel 9:
Gesundheit und Sicherheit am Arbeitsplatz
- Kapitel 10: Elektrische Dokumentation
- Kapitel 11: Pneumatische Dokumentation
- Kapitel 12: Allgemeine Anweisungen
- Kapitel 13: Anhänge
- Kapitel 14: Zusätzliche Maschinendokumente
Für weitere technische Informationen zu diesem Gerät rufen Sie unser Resolution Center unter 1-855-888-WELD an oder senden Sie eine E-Mail an service@weldmaster.com.
1.0 Überblick über die Maschine / Verwendungszweck
Die RFlex Presse ist die kleinste Maschine in unserer Hochfrequenz-Maschinenreihe. Sie ist robust konstruiert und auf Genauigkeit und lange Lebensdauer ausgelegt und verfügt über einen sehr robusten Montageschlitten mit Stahlkopf, der mit einem doppelten "V"-Mechanismus versehen ist.
Für "Nahtarbeiten" wird eine kleine Werkzeughalterung empfohlen, um gute Sicht und Zugang zum Arbeitsbereich zu gewährleisten. Für andere Anwendungen kann eine große Halterung geliefert werden, die eine starre Abstützung über einen großen Werkzeugbereich bietet. Es sind auch Vorrichtungen zur Vergrößerung der Ausladung erhältlich, wenn überschüssiges Material hinter den Werkzeugen positioniert werden muss.
Die Maschine wird häufig in der Medizin-, Automobil- und Bekleidungsindustrie zum Schweißen kleiner Anbauteile wie Schläuche, Luft- und Flüssigkeitsventile, Haken, Tüllen, Platten usw. eingesetzt. RFlex Die Presse hat eine HF-Leistung von 0,5 bis 4 kW. Die Maschine ist das perfekte Werkzeug für die Hilfsproduktion, bei der Präzision, manuelle Bedienbarkeit, Langlebigkeit und Stärke im Vordergrund stehen. Miller Weldmaster stellt Qualität, Präzision, Effizienz, Sicherheit und einfaches Design immer an erste Stelle.
DIE WICHTIGSTEN MERKMALE DER MASCHINE:
- die routinemäßige Wartung der Maschine ist sehr einfach;
- kann die Pressung genau eingestellt werden;
- Der Hersteller hat den Notrufknopf auf dem Bedienfeld installiert;
- Die Maschine ist mit einer Signallichtsäule ausgestattet, um die Sicherheit des Bedieners bei eingeschalteter Maschine zu erhöhen;
- Der Bediener kann den Arbeitszyklus der Maschine über das berührungsempfindliche HMI-Panel programmieren und steuern;
- Mit dem Programmiertool kann der Bediener Parameter wie Schweißzeit und -leistung sowie die Abkühlzeit in das System eingeben;
- Mit Hilfe des auf der Maschine installierten HMI-Panels kann der Bediener viele Schweißprogramme für verschiedene Materialien speichern, ganz zu schweigen von denen, die für die Arbeit mit verschiedenen Elektrodenarten verwendet werden;
- die Maschine ist mit einer zusätzlichen Erdungselektrode ausgestattet, um den Benutzer vor der erhöhten nichtionisierenden HF-Strahlung zu schützen, die von der Maschine ausgeht;
- ZTG HF AutoTuning System™ - die Maschine ist mit einem automatischen Leistungsregelungssystem ausgestattet, um die Sicherheit des Bedieners zu erhöhen;
- ZTG SafeDOWN™ - die Maschine ist mit einem System ausgestattet, das den Bediener beim Absenken wirksam vor der Elektrode schützen soll;
- ZTG Flash™ - ein weiteres System der Maschine, das die Elektrode und das zu schweißende Rohmaterial vor möglichen Schäden durch einen Lichtbogenüberschlag schützen soll;
- Alle Maschinen haben die CE-Konformitätszertifikate erhalten
HOCHFREQUENZTECHNIK:
Beim Hochfrequenzschweißen, auch bekannt als Radiofrequenz- (RF) oder dielektrisches Schweißen, werden Materialien durch Anwendung von Radiofrequenzenergie auf die zu verbindenden Bereiche miteinander verschmolzen. Die entstehende Schweißnaht kann genauso fest sein wie die ursprünglichen Materialien.
Beim HF-Schweißen werden bestimmte Eigenschaften des zu schweißenden Materials genutzt, um in einem schnell wechselnden elektrischen Feld Wärme zu erzeugen. Dies bedeutet, dass nur bestimmte Materialien mit dieser Technik geschweißt werden können. Bei diesem Verfahren werden die zu verbindenden Teile einem elektromagnetischen Hochfrequenzfeld (meist 27,12 MHz) ausgesetzt, das normalerweise zwischen zwei Metallstäben angelegt wird. Diese Stäbe dienen während des Erhitzens und Abkühlens auch als Druckapplikatoren. Das dynamische elektrische Feld versetzt die Moleküle in polaren Thermoplasten in Schwingung. Je nach ihrer Geometrie und ihrem Dipolmoment können diese Moleküle einen Teil dieser Schwingungsbewegung in Wärmeenergie umwandeln und eine Erwärmung des Materials bewirken. Ein Maß für diese Wechselwirkung ist der Verlustfaktor, der temperatur- und frequenzabhängig ist.
Polyvinylchlorid (PVC) und Polyurethane sind die gebräuchlichsten Thermoplaste, die mit dem HF-Verfahren geschweißt werden können. Auch andere Polymere wie Nylon, PET, PET-G, A-PET, EVA und einige ABS-Harze können mit dem HF-Verfahren geschweißt werden, doch sind hierfür besondere Bedingungen erforderlich. So sind Nylon und PET schweißbar, wenn zusätzlich zur HF-Leistung vorgewärmte Schweißstäbe verwendet werden.
Das HF-Schweißen ist im Allgemeinen nicht für PTFE, Polycarbonat, Polystyrol, Polyethylen oder Polypropylen geeignet. Aufgrund der drohenden Einschränkungen bei der Verwendung von PVC wurde jedoch eine spezielle Polyolefinsorte entwickelt, die sich für das HF-Schweißen eignet.
Die Hauptfunktion des HF-Schweißens besteht darin, eine Verbindung zwischen zwei oder mehr Blechdicken herzustellen. Es gibt eine Reihe von optionalen Funktionen. Das Schweißwerkzeug kann graviert oder profiliert werden, um dem gesamten geschweißten Bereich ein dekoratives Aussehen zu verleihen, oder es kann eine Prägetechnik eingesetzt werden, um Schriftzüge, Logos oder dekorative Effekte auf den geschweißten Teilen anzubringen. Durch den Einbau einer Schneidkante neben der Schweißfläche kann das Verfahren gleichzeitig schweißen und schneiden. Durch die Schneide wird der heiße Kunststoff so weit zusammengedrückt, dass das überschüssige Material abgerissen werden kann; daher wird dieses Verfahren oft als Aufreißschweißen bezeichnet.
ACHTUNG: Der Hersteller haftet nicht für Schäden oder Verletzungen, die durch eine unsachgemäße Verwendung dieses Geräts entstehen.
ACHTUNG! Um die Maschine optimal und sicher nutzen zu können, lesen Sie bitte alle Anweisungen in dieser Betriebs- und Wartungsanleitung sorgfältig durch und befolgen Sie sie.
ACHTUNG: Alle Mitarbeiter, die in den Bereichen Arbeitssicherheit, Betriebsabläufe und Risiken der Schweißmaschine geschult sind, sowie die zur Bedienung der Schweißmaschine befähigten Personen werden vom Auftragnehmer aufgefordert, das beigefügte Formular mit ihrer leserlichen Unterschrift zu versehen.
ACHTUNG: Die Hochfrequenz-Schweißmaschine wurde in einer für Menschen mit Behinderungen ungeeigneten Ausführung konzipiert und hergestellt. Wenn die Maschine von behinderten Personen bedient werden soll, muss die Maschine nach Rücksprache mit dem Hersteller entsprechend angepasst werden.
2.0 Sicherheitsschilder und Piktogramme
2.1 Allgemeine Informationen
Um das Schweißgerät optimal und sicher nutzen zu können, lesen Sie bitte sorgfältig alle Anweisungen in dieser Betriebs- und Wartungsanleitung, insbesondere auch alle Warn-, Verbots-, Beschränkungs- und Ordnungshinweise und -schilder.
Auf der Grundlage der in diesem Betriebs- und Wartungshandbuch enthaltenen Informationen muss der Kunde Arbeitsplatzhandbücher für die Mitarbeiter ausarbeiten.
Der Auftraggeber haftet in vollem Umfang, rechtlich und materiell für alle Ereignisse, die sich aus der unzureichenden Kenntnis dieses Betriebs- und Wartungshandbuchs oder aus der Nichteinhaltung der Grundsätze der Arbeitssicherheit und des Gesundheitsschutzes ergeben.

ACHTUNG: Jede Person, die ein HF-Schweißgerät bedient, muss sich vor Beginn der Arbeiten mit der Betriebs- und Wartungsanleitung vertraut machen.
ACHTUNG: Jeder Empfänger oder eine vom Empfänger beauftragte Person ist auf der Grundlage der vorliegenden Betriebs- und Wartungsanleitung und der ordnungsgemäßen Beschaffenheit der Produktionstechnik obligatorisch fällig das WORKSTAND MANUAL für das Bedienpersonal herauszugeben.
ACHTUNG: Die Hochfrequenzschweißmaschine darf NUR von Arbeitnehmern bedient werden, die in der Wartung des Geräts und in der INDUSTRIESICHERHEIT unter besonderer Berücksichtigung der von der Maschine ausgehenden möglichen Gefahren geschult wurden.
ACHTUNG: Der Hersteller des Geräts empfiehlt dem Käufer, während der gesamten Lebensdauer des Geräts das vom Hersteller bereitgestellte geschulte Servicepersonal oder vom Hersteller autorisierte Serviceteams in Anspruch zu nehmen.
ACHTUNG: Der Hersteller empfiehlt dringend, das Schweißgerät nur in industrieller Umgebung zu installieren.
ACHTUNG: Die Maschine muss richtig nivelliert sein und einen festen Arbeitsplatz haben.
ACHTUNG: Ein unvorsichtiger Umgang mit der Maschine während des Transports (Bewegung) kann zu schweren Verletzungen oder Unfällen führen.
ACHTUNG: Der Generator wird mit der lebensgefährlichen Spannung des Stromnetzes 3 x220 VAC; 50 Hz betrieben. Das Gerät hat eine Hochspannung von bis zu 5000 VDC. Alle Wartungs- oder Schutzmaßnahmen dürfen nur von geschultem Personal mit den gesetzlich vorgeschriebenen Befugnissen durchgeführt werden.
ACHTUNG: Der Käufer muss für die ordnungsgemäße Ausführung und die regelmäßige Kontrolle der Schutzmaßnahmen gegen Stromschläge für jedes in Betrieb befindliche Gerät Sorge tragen. Die gesamte Verantwortung in dieser Angelegenheit liegt auf Seiten des Käufers.
ACHTUNG: Die Lampenspannung muss mit der im Datenblatt des Produkts angegebenen Spannung übereinstimmen - sie kann über Abzweigungen auf der Primärseite des Glühlampentransformators eingestellt werden.
ACHTUNG: Die Lampe muss nach der Installation etwa eine Stunde lang vorgewärmt werden.
ACHTUNG: Jegliche Arbeiten im Bereich der aktiven Presseinheit der Presse, wie z.B. Geräteaustausch, dürfen nur mit besonderen Vorsichtsmaßnahmen durch geschultes Servicepersonal durchgeführt werden.
ACHTUNG! Ein Notstopp der Maschine ist jederzeit durch Drücken der EMERGENCY-Taste möglich. STOP-Taste (die rote Taste auf gelbem Hintergrund).
ACHTUNG: Die Arbeitsumgebung der Maschine, der Boden und die Handgriffe müssen immer sauber und frei von Verunreinigungen, Fett oder Schlamm sein, um das Risiko eines Ausrutschens oder Sturzes so gering wie möglich zu halten.
ACHTUNG: Ziehen Sie den Netzstecker des Geräts, bevor Sie Zugangsklappen entfernen oder Türen öffnen. Alle Schutzvorrichtungen und Zugangsklappen müssen vor dem Betrieb des Geräts angebracht werden.
ACHTUNG: Die Temperatur der Elektrode beträgt bis zu 100 °C. Daher kann man sich bei Berührung verbrennen.
ACHTUNG: Die Lampe enthält Seltenerdmetalle und Seltenerdmetalloxide, die hochgiftig sind. Im Falle eines Bruchs muss die Lampe mit äußerster Sorgfalt und mit Hilfe eines Fachmanns entsorgt werden. spezialisiert Dienstleistungen.
ACHTUNG: Die Hochfrequenz-Schweißmaschine ist eine Quelle für nichtionische elektromagnetische Strahlung. Nach der Installation der Maschine beim Käufer muss eine Messung der nicht-ionischen Strahlung durchgeführt werden. Die Strahlungsmessungen sollten von einem autorisierten Unternehmen durchgeführt werden.
ACHTUNG: Hochfrequenzschweißmaschinen müssen an einem festen Arbeitsplatz arbeiten, da die Umsetzung neue Messungen der nichtionischen Strahlungsintensität erfordert.
ACHTUNG: Personen mit einem implantierten Herzschrittmacher dürfen sich nicht in der Zone mit aktiver Strahlung aufhalten..
ACHTUNG: Der Hersteller empfiehlt, keine schwangeren oder stillenden Frauen im Bereich der aktiven nichtionischen Strahlung zu beschäftigen.
ACHTUNG: Die Hochfrequenzschweißmaschine wurde in einer für Menschen mit Behinderungen ungeeigneten Ausführung konstruiert und hergestellt. Wenn die Maschine von behinderten Personen bedient werden soll, muss die Maschine nach Rücksprache mit dem Hersteller entsprechend angepasst werden.


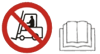

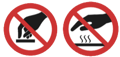



























3.0 Technische Daten
MaschineTyp |
ZD-NX-4 |
Materialien zum Schweißen |
PVC, PVC-beschichtete Gewebe |
Stromversorgung |
3 x 220 V; 50/60Hz |
HF-Ausgangsleistung |
4 kW |
PLC-Treiber |
Delta |
Steuerspannung |
24 VDC |
Installierte Kapazität |
6 kVA |
Anpassung der Ausgangsleistung |
Manuell/Autotuner |
Hauptausschnitt |
D25 A; verzögert |
Betriebsfrequenz |
27,12 MHz |
Frequenzstabilität |
+/- 0.6 % |
Antiflash-System, ZEMAT TG |
ultraschneller empfindlicher ARC-Sensor |
Druckluftverbrauch |
11 nl/Zyklus |
Größe des Arbeitstisches |
800 x 410 mm |
Schweißen Oberfläche |
100mm^2 |
Hub des Stellantriebs |
~ 100mm |
Antrieb der Presselektrode |
pneumatisch |
Antrieb der Masseelektrode |
pneumatisch |
Druckkraft (max) |
1200 kG |
Generatorlampe |
ITL 12-1 |
Kühlmittel |
Luft |
Gewicht der Maschine |
~ 3500 kg |
Abmessungen |
SEHEN ANHÄNGE |
4.0 Technische Beschreibung
Das Hauptelement der Hochfrequenzschweißmaschine ZD-NX-4 ist die tragende Struktur, die aus geschweißten Stahlblechen und -profilen besteht. Alle anderen Maschinenteile sind auf dieser Struktur montiert. Die tragende Struktur kann in zwei grundlegende Teile unterteilt werden:
- Auf der Rückseite befindet sich der Hochfrequenzgenerator zusammen mit dem Anodentransformator und dem Schaltkasten. Dieser Teil befindet sich in den abnehmbaren Abdeckungen, die durch den Endschalterschlüssel geschützt sind.
- die vordere, auf der sich der Arbeitstisch befindet, auf dem das geschweißte Material aufgestapelt wird. Die Schweißung wird ausgeführt, wenn die Elektrode durch die isolierte Klemme, die über die Zwischenplatte mit dem Fußhebel verbunden ist, gegen den Tisch gedrückt wird. Oberhalb des Tisches befindet sich ein Bedienfeld HMI
Die angebrachten Abschirmungen zusammen mit den Schalttasten sollen die Emission von nicht-ionisierender Strahlung minimieren. Das Betreiben des Schweißgerätes ohne die Abschirmung ist strengstens VERBOTEN!!!
- KONTROLLSYSTEM, bestehend aus PLC und HMI-Touchpanel, Steuerungs- und Handhabungskomponenten auf dem Hauptbedienfeld und anderen elektrischen und elektronischen Geräten auf der Maschine
- KOMPRESSORENDE LUFT besteht unter anderem aus einer Druckluftaufbereitungseinheit, Umschaltventilen und pneumatischen Stellantrieben.
- Der GENERATOR besteht aus einem hochfrequenten selbsterregten Generator mit Zerfallskonstanten, der hauptsächlich aus einer LC-Schaltung mit hohem Q-Faktor besteht, die auf 27,30 MHz eingestellt ist. Das System besteht auch aus der Wanderfeldröhre, dem Anodentransformator, dem Filamenttransformator und dem Röhrenkühlsystem;
Die angebrachten Abschirmungen zusammen mit den Schalttasten sollen die Emission von nicht-ionisierender Strahlung minimieren. Das Betreiben des Schweißgerätes ohne die Abschirmung ist strengstens VERBOTEN!!!
Die Maschine nutzt die folgenden Systeme vollständig aus:
- DIE STEUERUNG , bestehend aus der SPS mit dem berührungsempfindlichen HMI-Bedienfeld, den Bedienelementen und Anzeigen auf dem Hauptbedienfeld, das am Ausleger angebracht ist, und anderen elektrischen und elektronischen Geräten, die in dieser Maschine installiert sind; und
- DIE DRUCKLUFT-EINHEIT , die hauptsächlich aus der Druckluftaufbereitungsanlage mit Verteilerventilen und pneumatischen Stellantrieben besteht; und
- DER GENERATOR, bestehend aus einem hochfrequenten selbsterregten Generator mit Zerfallskonstanten, der hauptsächlich aus einer LC-Schaltung mit hohem Q-Faktor besteht, die auf 27,30 MHz eingestellt ist. Das System besteht auch aus der Wanderfeldröhre, dem Anodentransformator, dem Filamenttransformator und dem Röhrenkühlsystem;
Der Schweißelektrodenhalter ist mit einem automatischen Greifsystem ausgestattet, das über das HMI-Touch-Panel gesteuert wird. Es ermöglicht den werkzeuglosen Austausch der Elektroden.
Die angebrachten Abschirmungen zusammen mit den Schalttasten sollen die Emission von nicht-ionisierender Strahlung minimieren. Das Betreiben des Schweißgerätes ohne die Abschirmung ist strengstens VERBOTEN!!!
Zusätzlich sind am Fahrgestell der Maschine Laseranzeigen angebracht, die eine einfache Positionierung des geschweißten Materials auf dem Arbeitstisch ermöglichen.
5.0 Montage und Installation
5.1 Informationen und Hinweise auf Beschränkungen und Gebote
Der Hersteller sorgt für eine geeignete Verpackung der Maschine für die Zeit des Transports. Art und Haltbarkeit der Verpackung sind an die Entfernung und das Transportmittel und somit an das mögliche Risiko von Transportschäden angepasst. Der Hersteller schlägt vor, dass jeder Kunde die Transportmittel und das technische Servicepersonal des Herstellers nutzt.
Die Lagerung der Maschine stellt keine besonderen Anforderungen, abgesehen von einer geeigneten Lagerumgebung.
Der Lagerraum muss einen ausreichenden Schutz gegen Witterungseinflüsse gewährleisten, er sollte möglichst trocken sein und eine akzeptable Luftfeuchtigkeit aufweisen (unter 70 %). Außerdem muss ein angemessener Korrosionsschutz gewährleistet sein, insbesondere bei Metallteilen, die aus technischen Gründen nicht lackiert sind.
Wenn die Maschine in einer Schachtel geliefert wird und in Kunststoff eingewickelt ist, der eine korrosionsschützende Atmosphäre erzeugt, sollte die Maschine während der gesamten Lagerzeit eingewickelt und verpackt bleiben.
Zum Schutz vor Feuchtigkeit empfiehlt es sich, die Maschine nicht direkt auf dem Boden des Lagerraums, sondern auf Paletten zu lagern.
Ein Bauteil, das in jeder Phase - auch bei der Lagerung - besondere Aufmerksamkeit und Handhabung erfordert, ist die Generatorlampe (Triode). Die Lampe muss in ihrer Originalverpackung, in vertikaler Position, mit der Anode nach oben oder unten gerichtet, in einem trockenen Raum gelagert werden. Bei der Lampe handelt es sich um ein Hochvakuumbauteil aus Metall und Keramik, das äußerst zerbrechlich ist und auch aus geringer Höhe nicht gestoßen oder fallen gelassen werden darf.
Das Stoßen, Fallenlassen, Schütteln oder Kippen der Lampe über einen längeren Zeitraum kann und wird in der Regel zu einer dauerhaften und irreversiblen Beschädigung der Lampe führen. Insbesondere kann der Glühfaden der Lampenkathode gebrochen werden, was im Extremfall zu internen Kurzschlüssen oder zum Bruch der Lampe führen kann.
ACHTUNG: Die Lampe enthält Seltenerdmetalle und Seltenerdmetalloxide, die hochgiftig sind. Im Falle eines Bruchs muss die Lampe mit äußerster Sorgfalt und mit Hilfe von Fachdiensten entsorgt werden.
Die obigen Bestimmungen sollen alle Personen und Dienste, die mit diesem Gerät in Berührung kommen können, über dessen hohe Anfälligkeit gegenüber allen Impulsen und Schlägen belehren und warnen. Gleichzeitig werden im Rahmen des Reklamationsverfahrens keine Ansprüche im Zusammenhang mit den oben beschriebenen Dauerschäden anerkannt.
Es sollte auch betont werden, dass die Generatorlampe ein sehr teures Bauteil ist.
Im Falle von Zweifeln wird empfohlen, das Fachpersonal des Herstellers zu konsultieren.
5.2 Transport der Maschine
Die Partei, die für den Transport und die Installation der Maschine am Standort des Auftraggebers verantwortlich ist, sollte in der Phase der Vertragsunterzeichnung und spätestens nach der Endabnahme der Maschine am Standort des Herstellers bestimmt werden, bevor das Gerät an den Auftraggeber übergeben wird.
ACHTUNG: Ein unvorsichtiger Umgang mit dem Gerät während des Transports/Umzugs kann zu schweren Verletzungen oder Unfällen führen.
Es ist VERBOTEN, die Maschine von Personen montieren, demontieren oder transportieren zu lassen, die nicht über die entsprechenden Qualifikationen verfügen oder nicht mit den in dieser Betriebs- und Wartungsanleitung beschriebenen Sicherheitsanforderungen vertraut sind. Solche Handlungen können Unfälle oder Sachschäden verursachen.
In Anbetracht des spezifischen Charakters des Geräts empfiehlt der Hersteller jedem Auftraggeber, die Transportmittel und das technische Servicepersonal des Herstellers zu nutzen.
Die Leistungsröhre muss vor jedem Transport oder jeder Bewegung demontiert werden.
Die Leuchte muss immer in der Originalverpackung des Herstellers transportiert oder bewegt werden, in vertikaler Position, mit der Anode nach oben oder unten gerichtet, ohne dass die Leuchte gestoßen oder geschüttelt wird.
ACHTUNG: Die Maschine sollte in vertikaler Position transportiert werden.
Aufgrund der Größe und des Aufbaus der Maschine ist es erforderlich, einige Komponenten und Einheiten für die Zeit des Transports oder Umzugs zu demontieren und abzutrennen. Es ist notwendig, zerbrechliche und teure Bauteile und Werkzeuge zu demontieren (die in einem separaten Koffer transportiert werden sollten). Es ist unbedingt erforderlich, die Generatorlampe zu demontieren.
Die Maschine sollte mit Hilfe von Hebevorrichtungen - Kränen, Gabelstaplern, Palettenhubwagen - mit ausreichender Tragkraft bewegt werden, die einen sicheren Transport des Generators ermöglichen, wobei die Personen, die diese Hebevorrichtungen bedienen, über alle gültigen Lizenzen und gesetzlich vorgeschriebenen Qualifikationen verfügen sollten.
Alle Teile der Maschine, die während des Transports (wenn nicht ein Verpackungskarton mit hoher Widerstandsfähigkeit verwendet wird) oder durch Hebe- oder Transportvorrichtungen beschädigt werden könnten, sollten entsprechend gesichert werden (vorausgesetzt, sie werden demontiert und separat verpackt).
Um einen stabilen Stand des Geräts zu gewährleisten, ist es sehr wichtig, einen angemessenen Schutz der Maschine für die Zeit des langen Transports (Sicherheitsgurte, Verankerungsbolzen) sowie Schutz und Hilfe beim Transport auf der Baustelle zu gewährleisten.
Wenn die Maschine nicht mit entsprechenden Beschlägen ausgestattet ist, können auch andere verfügbare Löcher oder Elemente von ausreichender Haltbarkeit verwendet werden, um sicherzustellen, dass der Generator und andere Teile der Maschine richtig ausgewuchtet und stabilisiert werden.
Das Gewicht der Maschine (ca. 350 kg) muss bei der Planung des Transports unbedingt berücksichtigt werden.
5.3 Installation am Einsatzort
Je nach Komplexität der Maschine sollte die Installation am Einsatzort vom Personal des Bestellers, das diese Betriebs- und Wartungsanleitung gelesen hat, oder vom technischen Servicepersonal des Herstellers in Zusammenarbeit mit dem Personal des Bestellers durchgeführt werden.
Bitte denken Sie daran, dass die richtige Positionierung und Installation des Schweißgeräts von entscheidender Bedeutung ist, um seine optimale Funktion sowie den Komfort und die Sicherheit des Bedieners in der Umgebung des Geräts zu gewährleisten.
Der Auftraggeber ist verantwortlich für die Vorbereitung des Aufstellungsortes, die Verfügbarkeit und die Vorbereitung der elektrischen Anschlüsse sowie die Realisierung der besonderen Anforderungen der technischen Auslegung und der technischen Abnahmeprüfung, die den gesamten Generator für den Betrieb freigibt.
Der Hersteller wird dem Besteller alle diesbezüglich erforderlichen Anweisungen und Informationen zur Verfügung stellen.
ACHTUNG: Vergewissern Sie sich, dass der Boden / die Oberfläche / das Fundament, auf dem die Maschine aufgestellt werden soll, unter Berücksichtigung des Gewichts, der Oberfläche und der Verteilung des Maschinengewichts auf die Auflagepunkte (in der Regel die Beine) ausreichend haltbar ist.
ACHTUNG: Das Gerät muss ordnungsgemäß nivelliert sein und einen festen Platz für den Betrieb haben.
Der optimale Einsatzort des HF-Schweißgeräts ist die Betonoberfläche, die nicht oder nur mit einer sehr dünnen Schicht aus nichtleitendem Material bedeckt ist.
Die Oberfläche sollte in Übereinstimmung mit der jeweiligen Konstruktion unter Beachtung der Bau- und Sicherheitsnormen sowie der Anforderungen an parallele, senkrechte und ebene Positionen hergestellt werden.
ACHTUNG: Der Auftraggeber ist allein für die Erfüllung der vorgenannten Bedingungen verantwortlich.
Nach dem Aufstellen der Schweißmaschine am gewählten Ort ist es notwendig, die Maschine zu nivellieren, ihren technischen Zustand zu überprüfen und alle Mängel zu beseitigen, die während des Transports entstanden sein könnten. Anschließend wird der Generator ausgepackt, positioniert, nivelliert und befestigt. Die Lampe des Hochfrequenzgenerators sollte ganz am Ende des Installationsprozesses montiert werden. Diese Aufgabe muss mit besonderer Sorgfalt durchgeführt werden, sowohl beim Einsetzen der Lampe in die Fassung/den Sockel als auch beim Anschluss der elektrischen Kontakte der Lampe. Verbinden Sie die Stecker des Steuerpults mit den entsprechend gekennzeichneten Buchsen an der Presse. Es wird empfohlen, dass die Installation der Maschine nach dem Transport unter direkter Aufsicht eines Vertreters des Herstellers erfolgt.
ACHTUNG: Wenn die oben genannten Aufgaben von einem Vertreter des Kunden ausgeführt werden, müssen sie streng nach der Beschreibung in diesem Betriebs- und Wartungshandbuch und/oder den Anweisungen des Herstellers bei der technischen Abnahme durchgeführt werden.
Das Schweißgerät darf nur in Räumen verwendet werden, die frei von Staub, Säuren, Schwefel, ätzenden Dämpfen und brennbaren Gasen sind. Aufgrund des erzeugten Magnetfeldes sollten keine großen Metallgegenstände in der Nähe des Schweißgerätes platziert werden. Die Maschine kann den Betrieb elektronischer Geräte (Radio, Fernseher, Computer), die sich in der Nähe der Maschine befinden, beeinträchtigen, da diese Geräte sehr empfindlich auf Störungen reagieren. Der optimale Aufstellungsort für das Gerät ist eine Betonfläche, die nicht oder nur mit einer sehr dünnen Schicht aus nichtleitendem Material bedeckt ist.
5.4 Installation am Einsatzort
5.4.1 Installation am Einsatzort
ACHTUNG: Der Hersteller empfiehlt dringend, das Gerät nur in industrieller Umgebung zu installieren.
Die Maschine, die Gegenstand dieses Betriebs- und Wartungshandbuchs ist, wurde für den Einsatz in industrieller Umgebung zur Bearbeitung von Förderbändern entwickelt und hergestellt.
Die besonderen Betriebsbedingungen der Geräte, d. h. hohe Luftfeuchtigkeit, hohe Temperatur, Dampf und Staub, wurden von den Konstrukteuren der Maschine berücksichtigt und beeinträchtigen deren Betrieb nicht, sondern stellen strengere Anforderungen an die Durchführung von Präventionsprogrammen.
Die Maschine darf nicht in explosionsgefährdeten Bereichen, in stark staubhaltiger Atmosphäre, in Umgebungen mit hoher Luftfeuchtigkeit und/oder hoher Temperatur und bei Vorhandensein von aggressiven Dämpfen (säurehaltig, basisch, organisch oder anorganisch, mit potenziell oder tatsächlich korrosiver Wirkung) eingesetzt werden.
Die Temperatur der Arbeitsumgebung sollte zwischen +10º C und +40º C liegen und die relative Luftfeuchtigkeit zwischen 30% und 90%. Die Kondensation von Luftfeuchtigkeit oder aggressiven Substanzen auf der Oberfläche der Maschine (oder eines ihrer Bauteile) ist nicht zulässig.
Es ist erforderlich, dass die langfristige Temperaturamplitude während des Tages im Betriebsraum des Generators 10º C und im Falle der relativen Luftfeuchtigkeit 10% nicht überschreitet.
Die obige Klausel gilt nicht für Medien oder Stoffe, die zur Schmierung, Konservierung oder für nicht-aggressive Stoffe, die im Zuge der Herstellung/des Betriebs des Geräts verwendet werden.
ACHTUNG: Wenn ein großer Unterschied zwischen der Außentemperatur und der Temperatur in dem Raum besteht, in dem das Gerät aufgestellt ist, sollte das Gerät erst 24 Stunden nach seiner Aufstellung im Raum in Betrieb genommen werden.
5.4.2 Beleuchtung
Die Anforderungen an die Mindestlichtstärke besagen, dass auf der horizontalen Betriebsfläche die Beleuchtungsstärke, die in Räumen mit längerem Aufenthalt von Personen akzeptiert werden kann, unabhängig davon, ob visuelle Tätigkeiten ausgeführt werden, 300 lx betragen sollte.
Bei visuellen Tätigkeiten mit überdurchschnittlich hohem Schwierigkeitsgrad und hohem Sehkomfort sowie wenn die Mehrheit der Bediener über 40 Jahre alt ist, sollte die erforderliche Lichtstärke über dem Minimum liegen, d. h. mindestens 500 lx betragen.
5.4.3 Lärm
Die Maschine erzeugt keinen Lärm, der den Einsatz von Personenschutzmitteln oder -vorrichtungen erforderlich machen würde.
Es ist jedoch zu bedenken, dass alle Arbeitsumgebungen ihre eigenen Geräuschemissionen haben, die sich auf den Geräuschpegel auswirken können, den die Maschine während ihres Betriebs erzeugt.
5.5 Verbindungsparameter
5.5.1 Elektrische Energie
Anschluss: 3 x 2200V; 50Hz (3P+N+PE), Überstromschutz mit verzögerten Eigenschaften. Die Installation des Kunden muss Schutzmaßnahmen gegen elektrischen Schlag gewährleisten, die der EN 60204-1:2018-12 entsprechen.
ACHTUNG: Prüfen Sie nach dem Einbau der Röhre immer die Glühspannung - siehe technische Daten der Röhre.
5.5.2 Pressluft
Druck: 0,4 - 0,8 MPa, geforderte Reinheitsklasse nach ISO8573-1 4-4-4, Verbrauch: 11 nl pro Zyklus.
ACHTUNG: Wenn der Druck im System des Endverbrauchers höher als 0,8 MPa ist, muss er mit einem am Anschluss der Schweißmaschine montierten Reduzierventil auf etwa 0,8 MPa reduziert werden.
5.6 Verbindungsparameter
Abhängig von der Komplexität der Anlage und den Qualifikationen und Lizenzen der Mitarbeiter wird der Anschluss der Schweißmaschine am Einsatzort von Personen durchgeführt, die vom Auftraggeber ausgewählt wurden, oder von technischen Servicemitarbeitern des Herstellers in Zusammenarbeit mit dem Personal des Auftraggebers, gegen einen Aufpreis oder kostenlos, was immer vor der Übergabe der Maschine vom Standort des Herstellers an den Auftraggeber vereinbart wird.
Es ist immer zu prüfen, ob alle Anschlüsse entsprechend der Dokumentation des Gerätes vorgenommen wurden.
Es ist darauf hinzuweisen, dass die vorgenannten Aufgaben eine entsprechende Qualifikation des Personals erfordern, einschließlich entsprechender Lizenzen der zuständigen Stellen.
Sie gilt sowohl für fachliche Qualifikationen als auch für abgeschlossene und gültige Schulungen im Bereich Sicherheit und Gesundheitsschutz bei der Arbeit, insbesondere auch für die mit diesen Aufgaben verbundenen Risiken.
6.0 Betrieb
6.1 Vorbereitung der Maschine für den Betrieb - Erstinbetriebnahme
Kontrollverfahren vor der Operation:
- Kontrolle und Überprüfung der Wirksamkeit der Schutzmaßnahmen gegen Stromschlag
- Kontrolle und Überprüfung der Versorgungsspannung - Wert und Korrektheit des Phasenanschlusses, ggf. Drehrichtung des Motors
- die Spannung der Glühlampe überprüfen
- Entfernen Sie die Schutzabdeckungen des Schweißgeräts und prüfen Sie, ob es keine kleinen Beschädigungen gibt (keine gebrochenen Drähte, keine losen Verschraubungen usw.).
- Generatorlampen auspacken, überprüfen und installieren.
ACHTUNG: Um die Maschine optimal und sicher nutzen zu können, lesen Sie bitte alle Anweisungen in dieser Betriebs- und Wartungsanleitung sorgfältig durch und befolgen Sie diese.
Es ist VERBOTEN, Arbeiten an der Schweißmaschine durch Personen auszuführen, die nicht zuvor in der Bedienung von Hochfrequenzmaschinen und in den Arbeitsschutzbestimmungen unter besonderer Berücksichtigung der von der Maschine ausgehenden Gefahren geschult wurden.
Unter der Voraussetzung, dass alle Installationsvoraussetzungen erfüllt sind und die unter Punkt 5 beschriebenen Arbeiten durchgeführt wurden, sind wir bereit, die Schweißmaschine erstmals in der Produktionsumgebung des Auftraggebers in Betrieb zu nehmen.
ACHTUNG: Die erste Inbetriebnahme der Maschine sollte in Anwesenheit und unter Aufsicht von Vertretern des Herstellers erfolgen.
6.2 Betriebsanforderungen - Allgemeine Hinweise und Richtlinien
Alle Einstellungen und Kalibrierungen, die für die korrekten Betriebsparameter des Geräts erforderlich sind, wurden vom Hersteller während der Montage und der internen Testverfahren durchgeführt. Die allgemeine Konformität mit den vertraglichen technischen Anforderungen und der korrekte Betrieb der Maschine werden bei der technischen Abnahme bestätigt, die am Standort des Herstellers in Anwesenheit eines Vertreters des Auftraggebers und unter Verwendung von Original-Rohmaterial, das vom Auftraggeber zu Testzwecken geliefert wurde, stattfindet.
ACHTUNG: Aufgrund der spezifischen Eigenschaften der Geräte, die Hochfrequenzenergie aussenden, ist es notwendig, bestimmte Messungen am Einsatzort des Gerätes am Standort des Auftraggebers durchzuführen. Aus demselben Grund ist es sehr wichtig, dass die Maschine einen festen Betriebsort hat.
Vor der Inbetriebnahme der Maschine und der ersten Inbetriebnahme ist der Empfänger unbedingt verpflichtet, die Mitarbeiter zu schulen, die seine zukünftigen Bediener sind.
ACHTUNG: Die Schweißmaschine darf NUR von Arbeitnehmern bedient werden, die in der Wartung der Maschine und in der INDUSTRIESICHERHEIT unter besonderer Berücksichtigung möglicher von der Maschine ausgehender Risiken geschult wurden. Eine solche Schulung sollte durch ein entsprechendes, von einer geschulten Person unterzeichnetes Dokument bestätigt werden.
Darüber hinaus ist der Empfänger aufgrund der unterschiedlichen Arbeitszyklen unserer Maschinen in verschiedenen industriellen Umgebungen verpflichtet, eine klare und transparente BEDIENUNGSANLEITUNG für das Gerät zu erstellen, die an seine eigenen Produktionszyklen angepasst ist.
ACHTUNG: Der Käufer oder die von ihm beauftragte Person ist verpflichtet, auf der Grundlage dieser Betriebs- und Wartungsanleitung und der produktionstechnischen Merkmale ein WERKSTANDSHANDBUCH zu erstellen.
Aufgrund der spezifischen Eigenschaften der Geräte, die Hochfrequenzenergie aussenden, ist es notwendig, bestimmte Messungen am Einsatzort des Gerätes am Standort des Auftraggebers durchzuführen. Aus demselben Grund ist es sehr wichtig, dass die Maschine einen festen Betriebsort hat.
ACHTUNG: Die Hochfrequenz-Schweißmaschine ist eine Quelle für nichtionische elektromagnetische Strahlung. Nach der Installation des Geräts beim Käufer muss eine Messung der nicht-ionischen Strahlung durchgeführt werden. Die Strahlungsmessungen sollten von einem autorisierten Unternehmen durchgeführt werden und die Grenzen des Gefahrenbereichs festlegen.
ACHTUNG: Die Maschine muss einen festen Arbeitsplatz haben. Jede Änderung des Standortes des Gerätes erfordert entsprechende spezielle Messungen und die Bestimmung der Einwirkungszonen des nichtionisierenden elektromagnetischen Feldes.
VOR DEM BETRIEB UNBEDINGT ZU KONTROLLIEREN IST:
- Wirksamkeit von Schutzmaßnahmen gegen Stromschlag;
- Versorgungsspannung - Wert und Korrektheit der Phasenverbindung;
- Drehrichtung des Motors (falls zutreffend);
- Spannung der Glühlampe;
ACHTUNG: Die Lampenspannung muss mit der im Datenblatt des Produkts angegebenen Spannung übereinstimmen - sie kann über Abzweigungen auf der Primärseite des Glühlampentransformators eingestellt werden.
ACHTUNG: Aufgrund des spezifischen Charakters des Geräts ist es immer notwendig, das Personal über die hohe Versorgungsspannung der Anode der Lampe und das potenzielle Risiko eines tödlichen Stromschlags durch eine Spannung von bis zu 5000 VDC zu warnen und zu informieren.
ACHTUNG: Die Lampe muss nach der Installation etwa eine Stunde lang vorgewärmt werden.
- Position des Halters an der Basis des Arbeitstisches;
- Emission eines elektromagnetischen Feldes - nach der Einstellung der Schweißparameter, während des Schweißvorgangs;
EINBAU DER GENERATORLAMPE
- die seitliche Schutzabdeckung des Generators aus Lochblech entfernen
- das Kunststoffrohr, das den Luftstrom leitet, entfernen
- Setzen Sie die Lampe in die Fassung ein - die Lampe kann nur in einer Richtung in die Fassung eingesetzt werden (wenden Sie keine übermäßige Kraft an)
- das Kunststoffrohr montieren, das den Luftstrom leitet
- die Klammer für den Temperatursensor an der Anode anbringen und befestigen
- sicherstellen, dass der Endschalter des Schnursensors angebracht ist
- die Versorgungsplatten des Verteilerkondensators und des Scheibenkondensators am oberen Teil der Anode befestigen
- die Form oder Position der Metallteile in dieser Kammer des Generators nicht verändern
- das Stromversorgungssystem an das Stromversorgungsnetz anschließen und dabei die angemessene Qualität des Schutzsystems gegen elektrischen Schlag sicherstellen
- Schalten Sie den Glühkreislauf und das Steuergerät ein, indem Sie den HAUPTSCHALTER in die Position I-ON bringen. Die SUPPLY-Kontrollleuchte sollte aufleuchten (falls erforderlich, drücken Sie die blaue RESET-Taste auf der Steuerkassette);
ACHTUNG: Das Lampen-Kühlgebläse schaltet sich beim Einschalten des Glühkreises der Generatorlampe ein. Wenn das Gebläse nicht funktioniert, darf das Gerät nicht benutzt werden, bis die Störung des Gebläses behoben ist!!!
- Prüfen Sie die Glühspannung der Generatorlampe. Sie muss innerhalb des vom Hersteller der Triode vorgeschriebenen Bereichs liegen. Falls erforderlich, kann sie durch Änderung der Zweige des Transformators angepasst werden. Diese Arbeiten sollten von einem Vertreter des Maschinenherstellers oder (auf Risiko des Kunden) von einer anderen Person durchgeführt werden, die über die entsprechenden Qualifikationen verfügt, d. h. über ein Zertifikat des entsprechenden Elektrikerverbandes (in Polen SEP) und Kenntnisse über die Gefahren und Risiken, die mit dem Betrieb einer Hochfrequenz-Schweißmaschine verbunden sind, insbesondere das potenzielle Risiko eines Stromschlags durch die Spannung von bis zu 5000 V. Eine neue Lampe sollte etwa 0,5 Stunden lang brennen, bevor der Anodenkreislauf eingeschaltet wird.
- Testen Sie die Funktion des Steuergeräts nach dem unter Punkt 6 beschriebenen Verfahren.
- nach der Einstellung der Schweißparameter während des Schweißvorgangs die Emission des elektromagnetischen Feldes überprüfen.
WICHTIG: Wenn die Hochspannungskreise bei abgeklemmter Anode versehentlich angeschlossen wurden oder die Generatorlampe defekt ist, müssen die Hochspannungsfilterkondensatoren durch sehr kurzes Kurzschließen mit dem Gehäuse entladen werden.
ACHTUNG: Alle Tätigkeiten während der Inbetriebnahme und der Messungen, wenn das Sicherheitsniveau niedriger ist (offene Schutzschirme, blockierte Schlüsselschalter), müssen so wenig Zeit wie möglich in Anspruch nehmen, und das volle Sicherheitsniveau des Maschinenbetriebs muss so schnell wie möglich gewährleistet sein.
ACHTUNG: Alle Kontroll- und Messvorgänge müssen durchgeführt werden, nachdem überprüft wurde, ob sich die Schalter für die Einstellung der Anodenspannung in der Position 0 - OFF befinden (dies gilt nicht für die Messung der Emission des elektromagnetischen Feldes).
ACHTUNG: Alle Kontroll- und Messtätigkeiten dürfen nur von autorisiertem Personal durchgeführt werden.
Es ist IMMER VERBOTEN, den Schweißvorgang zu starten, d.h. die Hochspannung der Lampe einzuschalten, die die Hochfrequenzspannung an der isolierten Elektrodenhalterung auslöst, wenn das Sicherheitsniveau des Gerätebetriebs reduziert ist.
Die Maschine ist für den Betrieb im automatischen Zyklus ausgelegt. Der Automatikbetrieb ist die Standardbetriebsart des Geräts während des Produktionsprozesses.
Die Hochfrequenzschweißmaschine ermöglicht den Betrieb im manuellen Modus zu Einstellzwecken.
Maschinenbediener sollten immer normale Arbeitskleidung und rutschfeste Schuhe tragen.
Die Arbeitsumgebung des Geräts, der Boden und die Handgriffe müssen stets sauber und frei von Verunreinigungen, Fett oder Schlamm sein, um das Risiko eines Ausrutschens oder Sturzes so gering wie möglich zu halten.
Benutzen Sie die Arbeitsmaschine niemals ohne die festen oder beweglichen Schutzelemente. Kontrollieren Sie regelmäßig, ob alle Schutzgitter und alle anderen Schutzelemente richtig montiert sind und einwandfrei funktionieren.
Nur autorisierte Personen, die in der Bedienung der Maschine und im Arbeitsschutz geschult sind, dürfen direkten Kontakt mit der Maschine haben.
Jeder Bediener des Geräts muss über die Funktionen der Schutzelemente der Maschine und deren ordnungsgemäße Verwendung unterwiesen werden.
In der Umgebung des Geräts (ca. 1,5 m um den Generator und die Presse) dürfen sich keine Gegenstände befinden, die den Betrieb des Geräts stören könnten. Dieser Bereich muss sauber gehalten werden und über eine angemessene Beleuchtung verfügen.
Verwenden Sie niemals die Manipulatoren der Maschine oder flexible Rohre als Halterung. Denken Sie daran, dass jede versehentliche Bewegung des Gerätemanipulators versehentlich den Schweißprozess starten, die Parameter ändern oder sogar den Ausfall der Maschine oder die Beschädigung ihrer Werkzeuge verursachen kann.
Es ist MÜSSIG, die Aufsichtsperson und/oder das Verkehrspersonal über alle Fälle von Fehlbedienung des Geräts zu informieren.
ES IST STRENG VERBOTEN, Schutzabdeckungen zu entfernen, während die Maschine in Betrieb ist.
ES IST STRENG VERPFLICHTET, ALLE vorgesehenen Schutzabdeckungen und Sperrtasten zu verwenden.
Benutzen Sie die Arbeitsmaschine niemals ohne die festen oder beweglichen Schutzelemente. Kontrollieren Sie regelmäßig, ob alle Schutzgitter und alle anderen Schutzelemente richtig montiert sind und einwandfrei funktionieren.
In der Umgebung des Geräts (ca. 1,5 m um den Generator und die Presse) dürfen sich keine Gegenstände befinden, die den Betrieb des Geräts stören könnten. Dieser Bereich muss sauber gehalten werden und über eine angemessene Beleuchtung verfügen.
Die Arbeitsumgebung des Geräts, der Boden und die Handgriffe müssen stets sauber und frei von Verunreinigungen, Fett oder Schlamm sein, um das Risiko eines Ausrutschens oder Sturzes so gering wie möglich zu halten.
6.3 Für den Bediener verfügbare Bedienelemente und Anzeigen
Alle Bedienungs- und Anzeigeelemente des Schweißgeräts sind entweder an der Konstruktion oder am Bedienpult leicht zu finden. Bevor der Maschinenbediener mit der Arbeit beginnt, sollte er sich mit der Anordnung der Bedienelemente und Anzeigen an der Maschine sowie mit den Funktionen, die sie steuern, vertraut machen.
Die vollständige Liste der oben genannten Bedienungs- und Anzeigeelemente, die dem Bediener zur Verfügung stehen, ist unten beigefügt:
- HAUPTSCHALTER - der Schalter, der an der Vorderseite des Maschinengehäuses angebracht ist, dient zum Ein- und Ausschalten der Stromversorgung. Die Position 1- ON bedeutet, dass der Schalter eingeschaltet ist, während die Position 0-OFF bedeutet, dass der Schalter ausgeschaltet ist.
- LEISTUNGSSTAND - Der Umschalter ist an der Vorderseite des Maschinengehäuses angebracht. Der stufenweise Spannungsregler dient zur Einstellung der Anodenspannung Ua. Er schaltet die Zweige des Anodentransformators um (Der Schalter geht von 0 bis 1, 2, wobei: 0 - bedeutet, dass der Anodentransformator abgeschaltet ist, 1 - bedeutet, dass die Anodenspannung am niedrigsten ist, 2 - bedeutet, dass die Anodenspannung am höchsten ist).
- BEDIENFELD HMI - das PLC-Panel, bestehend aus einer Flüssigkristallanzeige, auf der die programmierten Schweißparameter zu finden sind, und den Schalttasten, die verwendet werden können, wenn die Parameter angezeigt werden sollen.
- EMERGENCY STOP - der rote Not-Aus-Taster mit Pilzkopf, mit dem die Maschine im Falle einer Störung oder eines Unfalls angehalten werden muss.
- USB - USB-Anschluss für die Übertragung von Rezepten und Alarmverläufen. Befindet sich auf dem Bedienfeld oder auf der rechten Seite der Maschine. Der Datenarchivierungsdienst wird in Kapitel 6.5 beschrieben. Der Anschluss ist eine Zusatzausstattung der Maschine.
- ANODENSTROM - das Strommessgerät, das sich auf der Schalttafel befindet (Abb. 8), misst den Strom im Anodenkreis und ermöglicht die visuelle Beurteilung des Schweißvorgangs (Lastcharakteristik des Generators).
- DRUCKEINSTELLUNG - Das handbetätigte Druckreduzierventil (Abb. 8) ist ein Ventil, das zur Druckeinstellung im Pneumatiksystem der Maschine dient (Ventil hochziehen und drehen: eine Drehung nach rechts - höherer Druck, eine Drehung nach links - niedrigerer Druck), der Nennbetriebsdruck der Maschine beträgt insgesamt 6 bar;
Der Druck im pneumatischen System darf nie höher sein als der Druck, der die Maschine antreibt.
- ANZEIGER FÜR DIE STELLUNG DES UNTEREN ENDSCHALTERS - eine Aussparung in der Platte mit einer Skala, die es ermöglicht, die Stellung des roten Anzeigers und damit die Stellung der Höhe des unteren Endschalters zu beobachten, was dessen Einstellung in der unteren Position erleichtert.
- RESET - der blaue Druckknopf, der sich auf dem Steuerpult befindet (Abb. 10), sollte verwendet werden, wenn die Maschine entweder aufgrund eines Unfalls neu gestartet oder eingeschaltet werden muss. Es wird dringend empfohlen, die Wiederholungsprüfung aller Alarmsysteme bei jedem Einschalten der Maschine durchzuführen.
- STOP - die schwarze Taste (Abb. 10), die sich auf der Kontrollstation befindet, sollte verwendet werden, um den Prozess des Hochfrequenzschweißens zu stoppen.
- START - Um die Hochfrequenzschweißung zu erreichen, müssen zwei grüne Drucktasten, die sich auf der Kontrollstation befinden (Abb. 10), betätigt werden (beide Drucktasten müssen gleichzeitig gedrückt werden).
- SIGNALLEUCHTSÄULE
- A. Die rote Farbe zeigt eine Störung an, und gleichzeitig sollte die Alarmmeldung auf dem berührungsempfindlichen Bedienfeld der HMI angezeigt werden.
Die Alarmmeldungen werden gelöscht und das rote Licht an der Signallichtsäule hört auf zu blinken, wenn die RESET-Taste gedrückt wird. Sollten die Bemühungen vergeblich gewesen sein und die Alarmmeldung nach Betätigung der RESET-Taste nicht gelöscht worden sein, so kann dies bedeuten, dass die Ursache für das Auftreten der Störung noch nicht beseitigt wurde.
- Orange Farbe zeigt an, dass der Hochfrequenzschweißer in Betrieb ist
- Die grüne Farbe zeigt an, dass die Maschine einsatzbereit ist.
- A. Die rote Farbe zeigt eine Störung an, und gleichzeitig sollte die Alarmmeldung auf dem berührungsempfindlichen Bedienfeld der HMI angezeigt werden.
- DRUCKLUFTAUFBEREITUNGSSYSTEM (Abb. 12) - besteht aus:
- den Druckluftanschluss, an den der Druckluftschlauch angeschlossen werden soll. Der Schlauch soll das System mit Druckluft im Bereich von 4 bis 8 bar versorgen
- das manuell betätigte Druckluftabsperrventil (um das Ventil zu öffnen, drehen Sie es nach links und stellen Sie es in die Position ON; eine Drehung nach rechts - die Position OFF - das Ventil ist geschlossen)
- das handbetätigte Druckreduzierventil ist ein Ventil, das zur Druckeinstellung im Pneumatiksystem der Maschine dient (Ventil hochziehen und drehen: eine Drehung nach rechts - höherer Druck, eine Drehung nach links - niedrigerer Druck), der Nennbetriebsdruck der Maschine beträgt 6 bar
Der Druck im pneumatischen System darf nie höher sein als der Druck, der die Maschine antreibt.
- der Druckluftfilter zusammen mit dem Kondenswasserablassmechanismus
- das Manometer, das die Höhe des Drucks im Druckluftsystem der Maschine anzeigt
- Elektrodenanpressbegrenzer - auf die Kolbenstange des Stellantriebs geschraubt, dient er zur Begrenzung des Längenhubs des Stellantriebs und soll verhindern, dass das Schweißmaterial unter der Elektrode "herausgequetscht" wird.
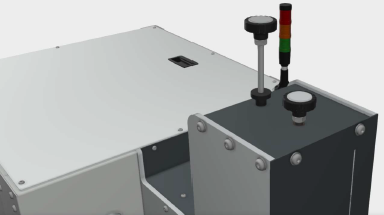
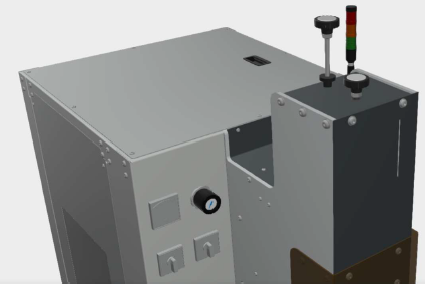
- Positionieren Sie das Material auf dem Arbeitstisch - wie beim Schweißen
- mit dem Fußhebel den Halter mit der Elektrode auf das Material absenken (so, dass die Elektrode das Material nur berührt, ohne Druck auszuüben) und stehen lassen
- Durch Drehen des Knopfes den Endschalter so verschieben, dass seine Rolle auf der Höhenanzeige der Elektrode steht. Den Drehknopf festziehen
- Heben Sie den Elektrodenhalter mit dem Fußhebel in seine obere Position
- Senken Sie die Elektrodenhalterung mit dem Fußhebel ab, drücken Sie die Elektrodenhalterung gegen das Material und prüfen Sie, ob die Schaltrolle an der Elektrode anhält.

Das Verfahren zur richtigen Einstellung des Höhenkontrollsystems:
- Positionieren Sie das Material auf dem Arbeitstisch - wie beim Schweißen
- mit dem Fußhebel den Halter mit der Elektrode auf das Material absenken (so, dass die Elektrode das Material nur berührt, ohne Druck auszuüben) und stehen lassen
- Durch Drehen des Knopfes (in Abb. 14 mit einem Pfeil markiert) den Endschalter so verschieben, dass seine Rolle auf der Höhenanzeige der Elektrode steht. Den Drehknopf festziehen
- Heben Sie den Elektrodenhalter mit dem Fußhebel in seine obere Position
- Senken Sie die Elektrodenhalterung mit dem Fußhebel ab, drücken Sie die Elektrodenhalterung gegen das Material und prüfen Sie, ob die Schaltrolle an der Höhenanzeige der Elektrode anhält und ob die Meldung auf dem HMI-Panel im Hauptfenster angezeigt wird.

6.5 Programmierung und Bedienung des berührungsempfindlichen Bediengeräts
ACHTUNG! Jeder Wert der in den Grafiken dieses Handbuchs dargestellten Parameter ist willkürlich gewählt und sollte vom Bediener der Maschine nicht beachtet werden. Die Werte der Parameter sollten aus der praktischen Erfahrung des Anwenders abgeleitet werden, da sie je nach Art des geschweißten Materials oder der eingesetzten Instrumente stark variieren können.
Im HMI-Panel werden alle editierbaren Werte der Parameter auf weißem Hintergrund angezeigt. Um einen Parameter anzuzeigen, muss der Benutzer auf seinen Wert drücken, woraufhin die Bildschirmtastatur geöffnet wird. Die Daten können durch Drücken der Eingabetaste gespeichert werden.
6.5.1 Anschluss an die Stromquelle
Kurz nachdem die Maschine an eine Stromquelle angeschlossen wurde, erscheint auf dem HMI-Display ein Alarmfenster mit der folgenden Meldung:
#K001 DRUCKKNOPF ZUM ZURÜCKSETZEN
In dieser Situation muss die Maschine neu gestartet werden, also muss die blaue RESET-Taste gedrückt werden. Dann muss man 30 Sekunden warten, bis die Maschine wieder betriebsbereit ist und in den Stand-by-Modus übergeht, was man an der folgenden Abfolge von Ereignissen erkennt: eine Leuchtanzeige in der Lichtsignalsäule blinkt grün und der blaue Fortschrittsbalken am oberen Rand des Fensters der HMI-Tafel verschwindet. Sollte die Alarmmeldung nicht von der HMI-Anzeige verschwinden, siehe Kapitel 6.5.2.
An prüfen, ob das Alarmsignal angezeigt wird, die
Taste auf der Oberseitedes Menüs gedrückt werden; wenn keine Meldungen vorhanden sind, wechselt die Grafik zu
6.5.2 Alarmmeldungen
Wenn eine Maschinenstörung auftritt oder wenn eines der Schutzsysteme eingeschaltet wird oder wenn andere Anomalien in der Funktion der Maschine festgestellt werden, wird eine der Alarmmeldungen auf dem berührungsempfindlichen Bedienfeld der HMI angezeigt. Alle Alarmmeldungen werden mit Hilfe der Taste RESTART gelöscht.

Die Arten von Alarmmassagen:
#K001 PUSH RESET BUTTON-diese Meldung zeigt an, dass die Ursache für mindestens eine der aktuell angezeigten Alarmmeldungen nicht mehr besteht. Drücken Sie die blaue RESET-Taste, um das Gerät in den Bereitschaftszustand zu versetzen.
#A001 EMERGENCY STOP - wird angezeigt, wenn:
- die Maschine ist eingeschaltet - der Sicherheitskreis der Maschine muss immer überprüft werden, wenn die RESET-Taste gedrückt wird
- der rote NOT-AUS-Taster mit Pilzkopf wurde gedrückt und hat sich verklemmt. Er muss durch Drehen des Kopfes nach rechts entriegelt werden.
#A002 TUBE TEMPERATURE - diese Meldung bedeutet, dass entweder die Kühlung des Laufwellenrohrs nicht vorhanden ist oder dass das Kühlsystem versagt. Sie wird angezeigt, wenn das thermische Schutzsystem des Rohrs in Betrieb ist, was bedeutet, dass sich das Laufwellenrohr auf eine zu hohe Temperatur erwärmt hat und infolgedessen der Splint des Rohrbands, der durch eine Schnur mit dem Endschalter verbunden war, ausgelötet wurde.
Ein Splint wird mit Hilfe eines Lotes, dessen Schmelzpunkt viel niedriger ist als der, bei dem die Röhre überhitzt (beschädigt) wurde, an ein Röhrenband gelötet. Wenn die Temperatur der Lampe zu stark ansteigt, fällt der Splint aus dem Band heraus, und als Folge davon wird der Endschalter ausgelöst, gleichzeitig wird die Alarmmeldung angezeigt und die Stromzufuhr für ein Glühen in der Röhre wird unterbrochen. Dann sollte die Ursache der Überhitzung beseitigt werden.
ACHTUNG! Das Kabel darf nicht an anderen Teilen der Maschine befestigt werden, sondern nur am Splint des am Rohr angeschraubten Bandes. Die Nichtbeachtung des genannten Hinweises kann zu einer Blockierung des Endschalters führen, was eine Überhitzung des Wanderfeldröhrchens und in der Folge dessen Beschädigung zur Folge haben kann.
If the cotter pin gets separated from the band, the band should be taken off from the tube, the pin should be soldered to the band with the standard solder used in electronic engineering (Melting point <190oC) so that the repaired part could be reattached to the tube.
Die Überhitzung der Röhre kann verursacht werden durch:
- der Schmutz, der sich entweder im Generator oder im Rohrheizkörper befindet
- der Ausfall des Röhrenkühlgebläses oder der Ausfall des Gebläsestromversorgungssystems
- die Verstopfung der Belüftungsöffnungen der Maschine oder die übermäßige Ansammlung von Erde durch die in den Belüftungsöffnungen installierten Filter
- die zu hohe Umgebungstemperatur.
#A003 ANTIFLASH - diese Art der Meldung bedeutet, dass das Schutzsystem gegen einen Lichtbogenüberschlag beim Schweißen ausgelöst wurde - vergewissern Sie sich aufgrund dieser Meldung, dass weder die Isolierunterlage, das geschweißte Material noch die Schweißelektrode beschädigt worden sind.
#A004 ANODE OVERLOAD - diese Meldung bedeutet, dass der Grenzwert für den Anodenanstieg überschritten wurde, so dass die Parameter für die beim Schweißen freigesetzte Leistung angepasst werden müssen.
#A006 NIEDRIGER LUFTDRUCK - diese Meldung bedeutet, dass der Luftdruck im pneumatischen System zu niedrig ist oder zu niedrig ist. Vergewissern Sie sich, dass der Schlauch, der die Druckluft liefert, an die Maschine angeschlossen ist, oder dass das Niveau der Druckluft angemessen ist, und stellen Sie dann mit Hilfe des Druckreduzierventils, das sich im Druckluftaufbereitungssystem befindet, den Druck in der Maschine auf das angemessene Niveau ein.

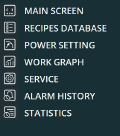





6.5.4 Hauptbildschirm
Rezept - Unter dieser Bezeichnung findet sich eine Gruppe von Parametern, die sich auf den Arbeitszyklus beziehen. Sobald die Schweißparameter für das jeweilige Produkt aus der Praxis ermittelt sind (die Werte der Parameter hängen stark von der Größe der Schweißnaht, der Größe des geschweißten Materials und der Form der Elektrode ab), sollten sie in das System eingegeben und unter dem Namen des Rezepts gespeichert werden.
Zusätzlich sind auf dem HMI-Display neben dem Namen jedes Parameters zwei Werte zu sehen. Der erste (auf blauem Hintergrund) ist der Wert des aktuellen Betriebsparameters, der in der aktuellen Zeit angezeigt wird, der zweite (auf weißem Hintergrund) ist der Sollwert, der aus dem Produktionsrezept oder den Daten des Bedieners stammt.
Bei Bedarf kann der Bediener jederzeit die Ziffer auf dem weißen Hintergrund drücken und ihren Wert ändern. Der Wert des aktuellen Betriebsparameters wird sofort aktualisiert, die Änderung hat jedoch keinen Einfluss auf das ausgeführte Rezept.
Um die auf dem Hauptbildschirm vorgenommenen Änderungen an einem Rezept zu speichern, drücken Sie die Taste SAVE RECIPE
um die Parameter aus dem Hauptbildschirm in die Leiste Rezept bearbeiten im Fenster Rezeptdatenbank zu kopieren. Die kopierten Parameter können über die Schaltfläche Neu erstellen als neues Rezept gespeichert oder über die Schaltfläche Aktualisieren zur Aktualisierung eines bestehenden Rezepts verwendet werden.
Name: - Der Name des Rezepts, der zu Produktionszwecken verwendet wird.
Anfangsleistung - dieser Parameter gibt die Position (Kapazität) des Ausgangskondensators im Generator an; die Anodenstromstärke in der Anfangsphase des Hochfrequenzschweißens hängt stark vom Wert dieses Parameters ab. (Der Parameter wird in Prozentwerten ausgedrückt, wobei 0% den niedrigsten Wert der Kapazität - die niedrigste Anodenstromstärke - und 100% den höchsten Wert der Kapazität - die höchste Anodenstromstärke - angibt).
-
Der Wert des Parameters Anfangsleistung und der Wert des Anodenstroms (im Material freigesetzte Leistung) sind nicht linear voneinander abhängig, so dass bei der Einstellung der Werte dieses Parameters entsprechende Vorsichtsmaßnahmen getroffen werden sollten.
Der aktuelle Wert des Parameters Ausgangsleistung und der Wert des eingestellten Parameters sind nur in der Anfangsphase des Schweißvorgangs gleich. Wenn das Verfahren eingeleitet wird, wird die Position des Ausgangskondensators automatisch angepasst, um die Betriebsleistung zu erreichen.
Betriebsleistung - dieser Parameter gibt den für das Schweißen verwendeten Anodenstrom I an. (Der Parameter wird in Amperewerten von 0 bis 4 A ausgedrückt).
Werte in grüner Farbe auf der Skala des Anodenstrommessgeräts zeigen die zulässigen Werte des Anodenstroms Ia an.
Wenn der Schweißvorgang eingeleitet wird, wird der Ausgangskondensator (Anfangsleistung) automatisch so eingestellt, dass die Betriebsleistung erreicht wird.
Verzögerungszeit - Dieser Parameter gibt die Zeit an, in der die Elektrode an dem geschweißten Material anhaftet, bevor die Schweißung ausgelöst wird. (Der Parameter wird in Sekunden ausgedrückt und reicht von 0 bis 99 s.)
Schweißzeit - dieser Parameter gibt die Zeit an, die die Maschine für die Bearbeitung der Hochfrequenzschweißung benötigt. (Der Parameter wird in Sekunden ausgedrückt und reicht von 0 bis 99 s.)
Abkühlzeit - dieser Parameter gibt die Zeit an, in der die Elektrode nach Beendigung der Schweißung gegen das geschweißte Material gedrückt wurde - das Material kühlt ab, während es gegen den Tisch gedrückt wird. (Der Parameter wird in Sekunden ausgedrückt und reicht von 0 bis 99 s.).
Strommodus: 1 - Der Schweißmodus des Stromtyps bedeutet, dass der Zähler der Maschine mit der Zählung der Schweißzeit der Hochfrequenz beginnt, die im Parameter Schweißzeit eingegeben wurde, sobald die Maschine den entsprechenden Wert des Anodenstroms La erhält, der entweder größer oder gleich dem im Parameter Betriebsleistung eingegebenen Wert sein sollte. Anders ausgedrückt, im Schweißmodus des Stromtyps ist die Schweißzeit gleich der Summe aus dem Wert der Zeit, die die Maschine braucht, um den Anodenstrom zu erzeugen (der im Parameter Betriebsleistung eingegebene Wert) und dem im Parameter Schweißzeit eingegebenen Wert.
Wenn das Gerät nicht in der Lage ist, innerhalb von 25 Sekunden die Betriebsleistung zu erreichen, beginnt es, die Heizzeit herunterzuzählen, beendet dann den Zyklus und zeigt schließlich eine Meldung an, dass die Betriebsleistung nicht erreicht wurde.
0 - Der Schweißmodus "Zeit" bedeutet, dass die Schweißzeit der Hochfrequenz dem Wert entspricht, der in den Rezeptparametern unter dem Namen "Schweißzeit" eingegeben wurde.
Es ist erwähnenswert, dass im Schweißmodus des Zeittyps der Arbeitszyklus auch dann ausgeführt werden kann, wenn die Maschine nicht in der Lage ist, die Betriebsleistung zu erzeugen, was dazu führt, dass die erzielte Schweißnaht eine ungleichmäßige Festigkeit aufweisen kann.
Kondensatorregelung:
1 - bedeutet, dass der Ausgangskondensator während des Schweißens automatisch so eingestellt wird, dass der Anodenstrom auf dem im Parameter Betriebsleistung eingestellten Niveau liegt.0 - signalisiert, dass die Maschine im Modus der begrenzten automatischen Anpassung des Ausgangskondensators arbeitet. Während des Schweißens wird der Ausgangskondensator nur eingestellt, wenn der Anodenstrom den im Parameter Power max eingegebenen Wert überschreitet.
Wenn Sie mit der Kondensatorregelung - 0 arbeiten, beachten Sie, dass die Maschine bei einer zu geringen Ausgangsleistung nicht in der Lage ist, den Anodenstrom Ia automatisch nach oben zu regeln, um den im Parameter Anodenstrom eingestellten Wert zu erreichen.
Leistungskorrektur - dieser Parameter bezieht sich auf die Methode zur Steuerung des Ausgangskondensators in der Anfangsphase, wenn nach dem Einschalten des Schweißzyklus der Kondensator den Betriebsstrom erreichen soll. Der Parameter ermöglicht es, die Kondensatorregelung zu deaktivieren, ohne den eingestellten Betriebsstrom zu erreichen.
- Beispiel 1: Der eingestellte Arbeitsstrom ist 1A, die Startposition ist 40%, die Kondensatorregelung ist 1, die Leistungskorrektur ist 0A.
- Nach dem Einschalten des Schweißzyklus beträgt der Betriebsstrom 0,5 A.
- Die Anpassung des Ausgangskondensators beginnt, um den angestrebten Betriebsstrom von 1A zu erreichen.
- Die Stellung des Kondensators ändert sich von 40 % auf 75 % - Der Betriebsstrom erreicht den Wert 1 A; die Einstellung des Kondensators wird beendet.
- Der Schweißzyklus wird fortgesetzt.
- Beispiel 2: Der Betriebsstrom ist auf 1 A eingestellt; die Startposition ist auf 40% eingestellt; die Kondensatorregelung ist auf 1 eingestellt; die Leistungskorrektur ist auf -0,2 A eingestellt.
- Nach dem Einschalten des Schweißzyklus erreicht der Betriebsstrom einen Wert von 0,5 A.
- Die Anpassung des Ausgangskondensators beginnt, um einen Zielbetriebsstrom von 1A abzüglich des Leistungskorrekturwerts zu erreichen, der 1A - 0,2A = 0,8A beträgt.
- Die Position des Kondensators ändert sich von 40% auf 60% - Der Betriebsstrom wird auf 0,8 A erhöht; die Kondensatoranpassung wird beendet.
Der Parameter Leistungskorrektur wird bei Schweißprozessen verwendet, bei denen der Arbeitsstrom in der Anfangsphase niedrig ist, gefolgt von einem sehr dynamischen Anstieg des Stroms. Die Überlagerung des spontanen Anstiegs des Arbeitsstroms und der Regulierung des Kondensators, die dessen Anstieg verursacht, führt zu einem unzulässig hohen Wert des Arbeitsstroms. Wird die Einstellung des Ausgangskondensators abgeschaltet, bevor der eingestellte Wert des Betriebsstroms erreicht ist, kann der Strom spontan den erforderlichen Wert erreichen.
Bei den meisten Schweißverfahren ist die Leistungskorrektur nicht erforderlich; der Parameter sollte dann auf 0 gesetzt werden.
Die Parameter des Rezepts - Leistungsstufe und Druck - mit dem gelb dargestellten Kommentar (MANUELL EINSTELLEN) sind nur eine Information für den Bediener, der, während er die Parameter auf dem Touchscreen liest, die Einstellungen an der Seite der Maschine manuell ändern muss. Eine Änderung dieser Einstellung auf dem Bildschirm hat keinen Einfluss auf die Maschineneinstellungen!
Leistungsstufe - ist die Haupteinstellung der Leistung der Maschine; die Einstellung erfolgt durch Änderung der Anodenspannung Ua im Bereich von 1 bis 2, wobei 1 für geringe Leistung und 2 für maximale Leistung steht: 0 - der Anodentransformator ist abgeschaltet.
ACHTUNG! Es ist wichtig, daran zu denken, dass trotz der Tatsache, dass die oben genannten Parameter unter dem Namen des Rezepts im berührungsempfindlichen HMI-Panel gespeichert werden können, es auch zwei andere Parameter gibt, wie z.B.: DRUCK und ELEKTRODEN-TEMPERATUR, die manuell eingestellt werden müssen.
Der Wert der Anodenspannung Ua sollte experimentell in Abhängigkeit von der Oberfläche der Schweißnaht und der Art des Schweißmaterials gewählt werden.
DRUCK - - der Parameter gibt den Druck der Druckluft im pneumatischen System der Elektrodenspannung an, ausgedrückt in bar im Bereich von 0 - 6 bar; der Parameter bestimmt die Anpresskraft der Elektrode im Verhältnis zum Material während des Schweißens.
Der Druck im pneumatischen System, mit dem die Elektrode gegen den Tisch gepresst wird, darf nie höher sein als der Druck, der die Maschine antreibt.
Nach der Einstellung der Leistungsstufe und des Drucks auf dem HMI-Panel im Hauptbildschirm wird ein Fenster angezeigt (Abb. 17), das den Bediener darauf hinweist, dass dieser Parameterwert manuell (mit einem entsprechenden Schalter) eingestellt und mit der Bestätigungstaste bestätigt werden muss.
Alarm Elektrode in unterer Position wird angezeigt, wenn die Elektrode die untere Position erreicht (Bewegung auf dem Sensor)
Durchgeführte Zyklen: - ist der Zähler der auf der Maschine ausgeführten Schweißzyklen. Hält der Bediener die Taste Taste zum Zurücksetzen des Zählers
3 Sekunden lang gedrückt halten, wird der Zähler zurückgesetzt.
ALARMMELDUNGEN, DIE DARÜBER INFORMIEREN, DASS KEINE BEDINGUNGEN FÜR DEN START DES SCHWEISSZYKLUS VORLIEGEN:
NICHT BEREIT - signalisiert, dass das Gerät nicht korrekt neu gestartet wurde und keinen Startvorgang von einigen Sekunden Dauer durchlaufen hat. Drücken Sie die Taste RESET auf dem Bedienfeld. Der Startstatus, d. h. die Aufwärmzeit der Lampe, wird als Fortschrittsbalken oben auf dem Bildschirm angezeigt.
6.5.5 Rezepturdatenbank
Datenbank mit Rezepten.
Alle im Speicher des HMI-Panels gespeicherten Rezepte werden in Form einer Spalte RECIPE LIST dargestellt. Die Rezeptparameter sind im vorherigen Kapitel beschrieben. Die Anzahl der Rezepte ist praktisch unbegrenzt. Der Inhalt des Rezepts wird auf der rechten Seite angezeigt; durch Anklicken der Werte auf dem weißen Hintergrund können die Parameterwerte geändert werden.
NEUES REZEPT: Um ein neues Rezept zu erstellen, füllen Sie alle Felder der Rezeptparameter aus und drücken dann die Taste
. Ein neues Rezept wird in der Rezeptliste angezeigt.
Um die Änderungen an einem Rezept zu speichern, die mit der Funktion Hauptbildschirmdrücken Sie die REZEPT SPEICHERN Taste
um die Parameter vom Hauptbildschirm in den Rezept bearbeiten Bar im Rezeptur-Datenbank Fenster. Die kopierten Parameter können als neues Rezept gespeichert werden, indem Sie die Neu erstellen oder sie können verwendet werden, um ein bestehendes Rezept zu aktualisieren, indem man die Schaltfläche Update Taste.
Wenn die Rezeptliste bereits ein Rezept mit demselben Namen wie das zu speichernde enthält, kann das neue Rezept nicht gespeichert werden, sondern es können nur die Parameter aktualisiert werden. Ändern Sie in diesem Fall den Namen des Rezepts.
REZEPT-EDITION
Um ein Rezept zu bearbeiten, müssen wir auf den Namen des Rezepts in der Rezeptliste klicken (das ausgewählte Rezept sollte gelb hervorgehoben sein und in Rezept bearbeiten Zeile). Soweit eine Änderung des Parameterwerts in Rezept bearbeiten Zeile betroffen ist, müssen wir auf das weiße Kästchen klicken, in dem es angezeigt werden soll, und einen neuen Wert eingeben. Sobald der Bearbeitungsvorgang abgeschlossen ist, wird die Update Taste muss gedrückt werden
und als Ergebnis werden die eingeführten Änderungen an dem angegebenen Rezept akzeptiert, gespeichert und abgelegt.
Um die Rezeptparameter vom Hauptbildschirm aus zu speichern, drücken Sie die Taste SAVE RECIPE
in diesem Fenster sichtbar. Wenn ein Rezept mit demselben Namen in der Rezeptliste vorhanden ist, werden seine Parameter aktualisiert.
LÖSCHVERFAHREN
Um das Rezept zu löschen, klicken Sie auf den Namen des Rezepts aus der Rezeptliste (das ausgewählte Rezept sollte gelb markiert sein und in der Zeile Rezept bearbeiten angezeigt werden) und drücken Sie dann die Taste Löschen.
REZEPTAUSWAHLVERFAHREN
Um die Rezepturauswahl für die Produktion durchzuführen, wählen Sie aus der Rezepturliste die Rezeptur mit den für die Einschaltdauer erforderlichen Werten aus (die ausgewählte Rezeptur ist gelb markiert und wird in Rezept bearbeiten Zeile), dann klicken Sie auf Belastung für die Produktion
Als Ergebnis wird das Rezept in das System hochgeladen und für die Verwendung in der laufenden Produktion vorbereitet, wobei die Parameter in der Hauptbildschirm Fenster.
SORTIERVERFAHREN
Die zur Herstellung verwendeten Rezepte sind in alphabetischer Reihenfolge aufgeführt. Bei einer größeren Anzahl von Rezepten erscheint seitlich der Tabelle eine Bildlaufleiste, mit der sich die Tabelle reibungslos durchblättern lässt. Es ist auch möglich, die Rezepte nach Namen, aufsteigend oder absteigend zu sortieren. Um die Rezepte zu sortieren, klicken Sie auf die Listenüberschrift - Rezeptliste; ein zweiter Druck ändert die Richtung der Sortierung. Alle Daten werden im Speicher des Bediengeräts gespeichert. Im Ordner "Recipe" befinden sich zwei Rezeptdateien: "Recipe.db" und "Recipe_a.rcp". Es ist möglich, Rezepte auf dem Computer zu bearbeiten. Es ist möglich, Rezeptdateien aus dem Speicher des Touchpanels auf einen USB-Stick zu kopieren und sie mit dem kostenlosen Programm EasyBuider Pro zu bearbeiten. Diese Dateien können als Sicherungskopie für Rezepte oder zum Hochladen von Rezepten auf ein anderes HMI-Touchpanel verwendet werden.
6.5.6 Leistungseinstellung
Leistungseinstellung.
Es gibt zwei Indikatoren in dem Fenster:
Anodenstrom - ein Indikator für die Anodenstromstärke. Sie zeigt die La-Anodenstromstärke an, die der Stromstärke des analogen Messgeräts entsprechen sollte, das sich auf dem Bedienfeld befindet.
KAPAZITOR - ein Werkzeug, das die Position des Ausgangskondensators anzeigt (im Bereich von 0 bis 100%). Mit Hilfe dieses Werkzeugs kann die Einstellung der entsprechenden Leistung erfolgen - in der Regel gilt: je größer die Kapazität, desto höher ist der La-Anodenstrom.
Eine Tastengruppe unter der Anzeige dient zur Einstellung des Anodenkondensators. Die Einstellung kann auf zwei Arten vorgenommen werden:
AUTO - vor dem Schweißen wird der Kondensator automatisch auf die Position eingestellt, die den in den Feldern Anfängliche Leistung Parameter. Wenn das Schweißverfahren ausgeführt wird, wird die Position des Kondensators automatisch so eingestellt, dass die Intensität des La-Anodenstroms auf den in der Tabelle angegebenen Wert steigen kann. Betriebsleistung Parameter.
Wählen Sie den AUTO-Einstellungsmodus für die von der Maschine ausgeführten Standardarbeitszyklen. Der Modus MANUELL wird für Testverfahren verwendet.
MANUELL - Der gesamte Einstellvorgang des Kondensators wird von Hand durchgeführt, bei Bedarf kann der Bediener die Position des Kondensators mit Hilfe von
oder
Tasten und gleichzeitig wird die Intensität des Anodenstroms eingestellt.
Leistung max. = Betriebsleistung + ... - der Parameter definiert den Maximalwert, um den die BETRIEBSLEISTUNG überschritten werden darf, um die automatische Absenkung des Anodenstroms unter Verwendung des Ausgangskondensators zu starten (Parameter definiert in Ampere, im Bereich von 0 - 1A). Leistung min. = Betriebsleistung - ... - der Parameter definiert den Mindestwert, um den die BETRIEBSLEISTUNG überschritten werden darf, um die automatische Erhöhung des Anodenstroms unter Verwendung des Ausgangskondensators zu starten (Parameter definiert in Ampere, im Bereich von 0 - 1A).
6.5.7 Arbeitsdiagramm
Arbeitsdiagramm.
Das Fenster enthält eine Grafik, die den Betrieb der Maschine im Detail zeigt. Es ist möglich, zwei Parameter zu beobachten, die sich in Echtzeit ändern:
- die Veränderungen des Anodenstroms (rote Linie);
- die Änderungen der Position des Ausgangskondensators (blaue Linie).
Das Diagramm zeigt Daten an, die in der Vergangenheit aufgezeichnet wurden. In der oberen rechten Ecke befindet sich eine Schaltfläche, die ein Fenster öffnet, in dem Sie den Zeitraum auswählen können, für den die Daten angezeigt werden sollen, und in dem Sie die Anzeigeeinstellungen des Diagramms ändern können.
6.5.8 Menü Service
- Beispiel 1: Der eingestellte Arbeitsstrom ist 1A, die Startposition ist 40%, die Kondensatorregelung ist 1, die Leistungskorrektur ist 0A.
-
Service-Menü.
In diesem Fenster werden die folgenden Informationen statistischen Ursprungs angezeigt:
Zykluszahl - das ist die Gesamtzahl der Arbeitszyklen seit dem ersten Einschalten der Maschine.
Arbeitszeit - das ist die Gesamtzeit der Maschinenarbeit,
Antiflash - dieser Wert gibt an, wie oft seit dem Tag der Herstellung der Maschine das Schutzsystem gegen Lichtbogenüberschlag eingeschaltet wurde.
Anodenüberlastungsalarm - dieser Wert gibt an, wie oft seit dem Tag der Herstellung der Maschine die maximale Stromstärke im Anodenkreis überschritten wurde und wie oft der Schutzmechanismus gegen Anodenüberlastung eingeschaltet wurde.
Netzüberlastungsalarm - dieser Wert gibt an, wie oft seit dem Tag der Herstellung der Maschine die maximale Stromstärke im Netzstromkreis während des Schweißens überschritten wurde und wie oft der Schutzmechanismus gegen Netzüberlastung daraufhin eingeschaltet wurde.
Röhrentemperaturalarm - dieser Wert gibt an, wie oft seit dem Tag der Herstellung der Maschine das Röhrentemperaturschutzsystem automatisch ausgelöst wurde.
Die unten aufgeführten Parameter sind nur für die Servicetechniker des Herstellers zugänglich, weshalb zum Bearbeiten der Parameter ein Passwort erforderlich ist.
Prozesssteuerung aktiv - aktiviert
oder deaktiviert
die Einstellungen der HF-Zyklussteuerung für den Arbeitsstrom (Anodenstrom) während des Schweißvorgangs. Mit anderen Worten, die Auswahl der Schaltfläche führt dazu, dass während des Schweißprozesses der +/- Toleranzbereich des Anodenstroms, der im Servicefenster in den Steuerungsparametern des Schweißprozesses angegeben ist, beachtet wird. Die Steuerungsparameter werden in diesem Handbuch näher beschrieben.
-
Power max = Betriebsleistung + - dieser Parameter gibt den Höchstwert der Stromstärke an, der den Wert der Betriebsleistungsgrenze überschreiten kann, um den automatischen Vorgang der Anodenstromabsenkung durch den Ausgangskondensator auszulösen (Parameter ausgedrückt in Amperewerten im Bereich von 0 bis 1A).
Leistung min = Betriebsleistung - . .. - Dieser Parameter wird nur zur Steuerung des Schweißprozesses und zur Bestimmung des unteren Bereichs der Stromtoleranz verwendet
-
Pressverzögerungszeit - dieser Wert gibt die Zeit an, die vom Auslösen des unteren Endschalters (der die untere Position der Elektrode anzeigt) bis zu dem Moment vergeht, in dem die Elektrode mit voller Kraft auf das Material gedrückt wird.
Einstellung % Schweißen in der Toleranz: - dieser Parameter gibt den prozentualen Wert der Zeit an, für die der Strom innerhalb der Toleranz liegen muss. Wenn der vorgeschriebene Prozentsatz nicht erreicht wird, wird auf dem HMI-Panel ein Alarm angezeigt, der darauf hinweist, dass die Schweißparameter nicht erreicht worden sind: #A013 SCHWEISSPARAMETER NICHT ERREICHT. In der Statistik wird in der Spalte Zyklusstatus 0 für den gerade ausgeführten Zyklus angezeigt.
Gesamtschweißzeit [s]: - dieser Parameter zeigt die Gesamtzeit an, die für die letzte Schweißung benötigt wurde.
Schweißzeit in der Toleranz [s]: - Dieser Parameter zeigt die Zeit der letzten Schweißung an; sie wird jedoch nur für den Strom innerhalb des in den obigen Parametern angegebenen Toleranzbereichs +/- (Power max/min) gezählt.
-
Prozentualer Anteil der Schweißung in der Toleranz [%] - Dieser Parameter zeigt den prozentualen Anteil der Zeit an, in der der Strom während des gesamten Zyklus, der kürzlich an der Maschine durchgeführt wurde, innerhalb des Toleranzbereichs +/- lag. Im Falle eines Alarms ist es möglich, schnell zu diagnostizieren, wie viel Prozent der Schweißzeit für die oben genannten Parameter erreicht wurde.
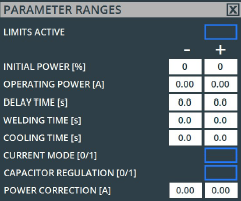



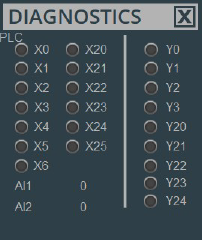


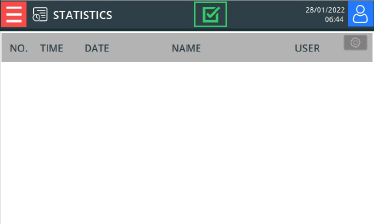
Zeit - Uhrzeit der Aufzeichnung
Betriebsleistung [A] - Wert des im Prozess verwendeten Parameters
Kondensatorregelung [0/1] - Wert des im Prozess verwendeten Parameters
- der Parameter Strommodus wurde auf 0 gesetzt - der Mittelwert wird ab dem Zeitpunkt des Einschaltens der Hochfrequenz gezählt
- der Parameter Strommodus ist auf 1 gesetzt - der Mittelwert wird ab dem Zeitpunkt gezählt, an dem der eingestellte Wert des Arbeitsstroms erreicht wurde;
Zykluszähler - Wert, der auf dem Zykluszähler ab der ersten Inbetriebnahme der Maschine angezeigt wird
BEDIENERANMELDUNG
Das Touchpanel kann gegen unbefugten Zugriff gesichert werden. Um die Funktion der Benutzeranmeldung zu aktivieren oder zu deaktivieren, gehen Sie zum Servicefenster und klicken Sie dann auf den unten rot markierten Bereich:
Das folgende Fenster wird geöffnet:
Aktiv anmelden - Schaltfläche aktiviert oder
schaltet die Protokollierung ab. Um zwischen den Funktionalitäten zu wechseln, muss das Passwort 21369 eingegeben werden.
Im Folgenden sind die Meldungen aufgeführt, die auf dem Rechner erscheinen, je nachdem, ob der Benutzer sich anmeldet, einen neuen Benutzer hinzufügt, einen Benutzer löscht, die Benutzerrechte oder das Kennwort ändert.
- Erfolg! (kann beim Einloggen, Hinzufügen neuer Benutzer, Löschen von Benutzern, Ändern von Benutzerrechten und Ändern des Passworts erscheinen).
- Falsches Passwort! (kann nur beim Einloggen erscheinen).
- Konto existiert bereits! (kann nur beim Hinzufügen eines Benutzers erscheinen).
- Inakzeptable Zeichen im Passwort! (kann beim Hinzufügen eines Benutzers und Ändern des Passworts erscheinen).
- Inakzeptable Zeichen im Namen! (kann nur beim Hinzufügen eines Benutzers erscheinen)
1. nach dem Einschalten des Geräts klicken Sie auf die Schaltfläche "Anmelden" auf dem Touchpanel-Fenster
2. Es öffnet sich ein kontextbezogenes Fenster zum Einloggen.
3. Wählen Sie einen geeigneten Benutzer aus der Dropdown-Liste aus.
4. Geben Sie das entsprechende Passwort ein und bestätigen Sie es mit der Eingabetaste auf der Tastatur.
5. Drücken Sie die Taste Log-in.
6. Eine entsprechende Meldung wird auf dem Bildschirm angezeigt.
Nach dem Ausschalten des Geräts wird der Benutzer automatisch abgemeldet.
ANLEGEN NEUER BENUTZER
1. Melden Sie sich als ein Benutzer an, der die Berechtigung zur Benutzerverwaltung hat.
2. Symbol auswählen
3. Geben Sie den Namen eines Benutzers in das Benutzerfeld ein (Buchstaben und Zahlen)
4. Geben Sie das Passwort in das Passwortfeld ein (Buchstaben und Zahlen)
5. Wählen Sie die Rechte, die der zu erstellende Benutzer haben soll.
A - grundlegende Arbeiten an der Maschine
B - nicht zugewiesen
C - Rezeptbearbeitung
D - nicht zugewiesen
E - nicht zugewiesen
F - Dienstparameter, Benutzerverwaltung
6. Wählen Sie die Schaltfläche Hinzufügen.
7. Eine entsprechende Meldung wird auf dem Bildschirm angezeigt.
LÖSCHEN VON BENUTZERN
1. Melden Sie sich als ein Benutzer an, der die Berechtigung zur Benutzerverwaltung hat.
2. Symbol auswählen
3. Wählen Sie einen geeigneten Benutzer aus der Dropdown-Liste aus.
4. Drücken Sie die Löschtaste.
5. Eine entsprechende Meldung wird auf dem Bildschirm angezeigt.
ÄNDERUNG DER DEM BENUTZER ZUGEWIESENEN BERECHTIGUNGEN.
1. Melden Sie sich als ein Benutzer an, der die Berechtigung zur Benutzerverwaltung hat.
2. Symbol auswählen
3. Wählen Sie einen geeigneten Benutzer aus der Dropdown-Liste
4. Wählen Sie die Berechtigungsstufe für einen bestimmten Benutzer aus oder heben Sie die Auswahl auf.
5. Drücken Sie Ändern.
6. Eine entsprechende Meldung wird auf dem Bildschirm angezeigt.
ÄNDERUNG DES PASSWORTS
1. Einloggen. Der Bediener kann nur sein eigenes Kennwort ändern; ein Vorgesetzter kann jedoch das Kennwort eines beliebigen Benutzers ändern
2. Symbol auswählen
3. Wählen Sie einen geeigneten Benutzer aus der Dropdown-Liste aus (wenn Sie als Supervisor angemeldet sind).
4. Geben Sie das neue Passwort ein
5. Drücken Sie Ändern.
6. Eine entsprechende Meldung wird auf dem Bildschirm angezeigt.
WERKSEITIG ANGELEGTE BENUTZER UND DEREN ZUGEWIESENES PASSWORT
BENUTZERNAME - PASSWORT
BEDIENER - 33
AUFSICHTSPERSON - 11
Miller Weldmaster - FÜR DEN SERVICE DES HERSTELLERS BESTIMMT;
Erlaubt:
OPERATOR - Arbeit an der Maschine, die Fähigkeit zur Auswahl und Bearbeitung von Rezepten.
SUPERVISOR - Arbeit an der Maschine, Auswahl eines Rezepts, Bearbeitung von Rezepten, Änderung von Parametern, Hinzufügen und Entfernen von Bedienern und Änderung der Passwörter anderer Benutzer.
Im Speicher des HMI-Touchpanels archivierte Daten

Zum Lesen und Konvertieren von Verlaufsdateien und Rezepten auf einem Computer mit Windows-Betriebssystem ist die folgende Software erforderlich:
- die kostenlose Software EasyBuider Pro, die von der HMI-Tafel auf der Website des Herstellers heruntergeladen werden kann: http://www.weintek.com/ oder bei der Vertretung in Polen http://www.multiprojekt.pl/ftp/weintek_hmi/easy_builder_pro/
- Microsoft Excel oder ein anderes Tabellenkalkulationsprogramm.
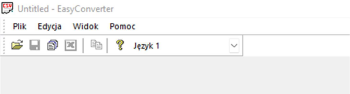
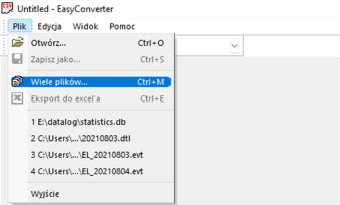
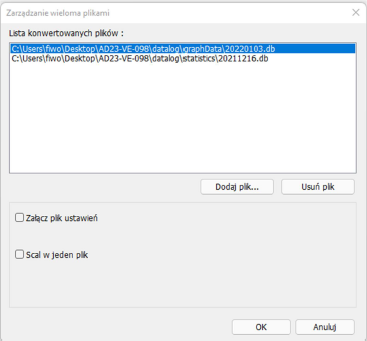
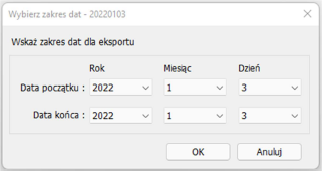
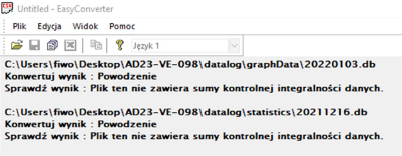
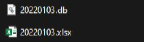
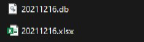
- Wählen Sie auf dem Computer, der mit einer drahtlosen Netzwerkkarte ausgestattet ist, das Netzwerk mit einem Namen aus, der der Fabriknummer des Geräts entspricht, wie sie auf dem Typenschild angegeben ist, zum Beispiel: D120-XM-003.
- Geben Sie das Passwort entsprechend der Werksnummer des Geräts in Großbuchstaben vom Ende her ohne Bindestriche ein, zum Beispiel: 300MX021D.
- Rufen Sie das Dienstfenster auf und klicken Sie auf den unten rot markierten Bereich.
- Es öffnet sich das Fenster mit den erweiterten Einstellungen, in dem die IP-Adresse des HMI-Panels und das aktuell geladene Projekt zu finden sind.
KOPIEREN VON VERLAUFSDATEIEN AUS DEM HMI-PANEL ÜBER DAS WI-FI-NETZWERK
- Öffnen Sie den Windows Explorer in einem beliebigen Ordner und geben Sie in der Adresszeile, in der sich die IP-Adresse befindet, folgende Formel ein, z. B.: 192.168.1.50; die vom Touch Panel abgelesene Adresse sollte eingegeben werden: ftp://uploadhis:753456@192.168.1.50/
- Klicken Sie dann auf 'Enter'.
- Ein Fenster mit dem Speicher des Touchscreens wird geöffnet
- Die Struktur der Ordner wurde in einem der folgenden Kapitel beschrieben. Der gesamte Inhalt jedes Ordners kann kopiert werden. Es ist auch möglich, einzelne Dateien zu kopieren, die in den Ordnern gespeichert sind.
IM SPEICHER DES HMI TOUCH PANEL ARCHIVIERTE DATEN
- Stecken Sie ein USB-Speichergerät in den Anschluss des HMI-Touchpanels.
- Auf dem Bildschirm des HMI-Bedienfelds erscheint ein Fenster, in dem angezeigt wird, dass die Taste Upload vor Ablauf des Countdowns gedrückt werden muss.
- Im nächsten Fenster wählen Sie die herunterzuladenden Daten aus und geben das Passwort ein:
- 753456, wählen Sie den Speicherort /usbdisk/disk_a_1 und klicken Sie auf die Schaltfläche Hochladen, um den Download der Dateien zu starten.
DIE STRUKTUR DER VERLAUFS- UND REZEPTDATEIEN
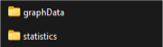
- "recipe" - im Ordner "recipe" gibt es drei Dateien: "recipe.db", "recipe_a.rcp" und "recipe.rcp". Die Datei "recipe.db" enthält die im HMI-Panel gespeicherten Rezepte. Sie kann als Backup oder zum Hochladen von Rezepten auf ein anderes HMI Touch Panel verwendet werden. Sie können Rezepte auch auf Ihrem Computer bearbeiten.
- "datalog" - im" datalog"-Ordner gibt es den" graphData"-Ordner und den" statistics"-Ordner.
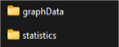
- "graphData" - im Ordner "GraphData" befinden sich Dateien, die Aufzeichnungen über die Betriebsparameter der Maschine enthalten. Für jeden Tag, an dem die Maschine betrieben wird, wird eine Datei mit dem Namen des Datums gespeichert. Außerdem wird Folgendes aufgezeichnet:
- C [%] - Position des Kondensators
- Ia [A] - Anodenstromstärke
Alle diese Parameter werden einmal alle 0,5 Sekunden und nur während des Zyklus gespeichert. Sie werden in einer Tabelle gespeichert.
- "Statistik" - im Ordner "Statistik" befinden sich Dateien mit Prozessstatistiken. Für jeden Tag, an dem die Maschine betrieben wird, wird eine Datei mit dem Namen des Datums gespeichert. Außerdem wird Folgendes aufgezeichnet:
- Rezeptname - Name des Rezepts, das zur Ausführung des aufgezeichneten Arbeitszyklus verwendet wird.
- user - Name des Bedieners, der während des Zyklus angemeldet ist.
- capa position [%] - voreingestellte Startposition des Kondensators.
- Strom [A] -Betriebsstrom eingestellt.
- delay time [s] -Verzögerungszeit eingestellt.
- Schweißzeit [s] - eingestellte Heizzeit.
- Kühlzeit [s] - eingestellte Kühlzeit.
- Leistungsstufe - eingestellte Leistungsstufe.
- Druck [bar] - eingestellter Druck.
- aktueller Modus - Sollwert des aktuellen Modus .
- Kondensatorregelung - Sollwert der Kondensatoreinstellung.
- aktuelle Korrektur - Wert des im Prozess verwendeten Parameters.
- Prozesssteuerung - Informationen zur aktiven Prozesssteuerung.
- Prozessstatus - Status der Prozesssteuerung, wobei -1 bedeutet, dass die Prozesssteuerung inaktiv ist,
- bedeutet Fehler - Prozess unterbrochen oder Schweißparameter nicht erreicht, 1 bedeutet Erfolg - der Schweißprozess ist gemäß den für den Strom eingestellten Parametern abgelaufen.
- aktueller Status - Status der aktuellen Steuerung, wobei -1 eine inaktive Prozesssteuerung bedeutet,
- bedeutet Fehler - Prozess unterbrochen oder Schweißparameter nicht erreicht, 1 bedeutet Erfolg - der Schweißprozess ist gemäß den eingestellten Parametern verlaufen.
- Durchschnittsstrom - durchschnittlicher Stromwert während des Schweißens.
- Zähler - Maschinenzykluszähler.
- eventlog" - im Ordner "eventlog" befinden sich Dateien mit einer Aufzeichnung der Historie der Alarmmeldungen, die während des Betriebs der Maschine angezeigt wurden. Die Historie der Alarmmeldungen wird in einer Datei mit dem Namen EL_data gespeichert, zum Beispiel: EL_20220105. Folgendes wird ebenfalls aufgezeichnet:
- Ereignis - Information, wobei 0 angibt, wann die Alarmmeldung aufgetreten ist und 2 angibt, wann die Alarmmeldung zurückgesetzt wurde
- Kategorie - unerheblich
- Nachricht - der Inhalt der Alarmmeldung
- Schließen Sie den USB-Speicher mit den gerippten Rezepten an den Computer an und öffnen Sie das Programm Utility Manager.
- Klicken Sie in der oberen linken Ecke des Fensters auf Bildschirm auswählen und wählen Sie das Panelmodell: cmt X Serie - Basic.
- Wählen Sie auf der Registerkarte Datenkonvertierung die Anwendung Rezepturdatenbank-Editor.
- Klicken Sie in der Anwendung Rezeptdatenbank-Editor auf Importieren... und wählen Sie die Dateien mit den kopierten Rezepten "recipe.db".
- Das Rezeptbearbeitungsfenster wird geöffnet.
- Wenn die Bearbeitung abgeschlossen ist, klicken Sie auf Exportieren... und speichern Sie die Datei an ihrem vorherigen Speicherort.
KOPIEREN VON REZEPTEN AUS DEM USB-SPEICHER:
- 1. Stecken Sie den USB-Stick mit den gespeicherten Rezepten in die Buchse des HMI-Touchpanels. Die Rezeptdatei muss sich genau so im Ordner "recipe" befinden, wie sie beim Herunterladen von Rezepten vom Bedienfeld ist
- Auf dem Bildschirm des HMI-Panels erscheint ein Fenster, klicken Sie auf Download.
- Im nächsten Fenster wählen Sie Rezeptdatenbank; wählen Sie den Speicherort der Rezeptdatei; geben Sie das Passwort ein: 753456 und klicken Sie auf die Schaltfläche Herunterladen.
Die Rezepte werden in den Speicher des HMI-Touchpanels geladen. Schalten Sie das Gerät aus und dann wieder ein.
6.6 Anschluss an die Stromquelle
Die Maschine darf unter keinen Umständen von unqualifiziertem Personal bedient werden. Die Bediener der Maschine müssen mit den Vorschriften für Sicherheit und Gesundheitsschutz am Arbeitsplatz vertraut sein.
Bevor das Gerät an eine Stromquelle angeschlossen wird, sollten die folgenden Schritte durchgeführt werden:
- sich vergewissern, dass die Arbeitsumgebung der Maschine (Maschine und Umgebung) sauber und in Ordnung ist oder dass keine Hindernisse vorhanden sind, die sich negativ auf den normalen Arbeitszyklus der Maschine auswirken können; und
- sicherstellen, dass eine angemessene Menge an Rohmaterial (Teststücke) vorbereitet wird; und
- sicherstellen, dass die Abfallbehälter und -container für geschweißte Produkte an der richtigen Stelle, aber in unmittelbarer Nähe der Maschine aufgestellt werden, um den Anforderungen des Bayer-Konzerns an den Produktionszyklus zu entsprechen.
- Die Schweißelektrode sollte auf einer Klemme installiert werden (die Ausnahme von der Regel ist, wenn die Elektrode auf das Material gelegt und dann durch eine Klemme gedrückt wird)
- Vergewissern Sie sich, dass alle Abdeckungen ordnungsgemäß an der Maschine befestigt und die Seitentüren eines Schaltkastens geschlossen sind;






- Heben Sie die Elektrode in ihre obere Position.
- Drehen Sie den HAUPTSCHALTER auf die Position 0-OFF - das bedeutet, dass die Maschine ausgeschaltet ist.
- Drehen Sie den Hand-Druckluftabsperrhahn ab (zur Durchführung des Verfahrens drehen Sie den Hahn nach rechts in die Position OFF)
- Bringen Sie die Arbeitsumgebung rund um die Maschine in Ordnung.
- Bei längeren Arbeitsunterbrechungen sollten sowohl der Stecker der Stromversorgung als auch der des Druckluftsystems herausgezogen werden (beide Stecker sollten aus den Steckdosen herausgezogen werden).
DIE EINSTELLUNG DER TISCHPARALLELITÄT
Falls die Parallelität zwischen der Schweißfläche der Elektrode und der Oberfläche des Arbeitstisches korrigiert werden muss, wird die Einstellung der Elektrodenposition mit Hilfe von Einstellschrauben empfohlen.
DIE EINSTELLUNG DES FUSSHEBELS
Die Vorwärts- oder Rückwärtsbewegung des Fußhebels kann mit Hilfe von Muttern eingestellt werden, von denen eine in Abb. 32 mit dem Buchstaben A gekennzeichnet ist. Die andere Mutter befindet sich auf der gegenüberliegenden Seite. Außerdem sind am Fußhebel auf beiden Seiten Löcher gebohrt, um den Fußhebel bei Bedarf abzusenken.
6.7 Prüf- und Einstellverfahren


Das Prüf- und Einstellverfahren sollte in der Praxis angewendet werden, wenn:
- das Gerät zum ersten Mal eingeschaltet wurde,
- der Austausch von Werkzeugen erforderlich ist (wenn sich der Bedarf ergibt),
- der Wartungsvorgang abgeschlossen ist,
- die Bediener müssen mit der Funktionsweise der Maschine vertraut sein.
Für die Durchführung des genannten Verfahrens sollte der Bediener:
1. Vergewissern Sie sich, dass der Schalter Ua SETTING, der sich an der Seite der Maschine befindet, in der Position 0 - OFF steht.2. Ordnen Sie das zu schweißende Material auf dem Arbeitstisch an.

3. Drücken Sie den Fußhebel und die Klemme mit der Elektrode auf das Material.

7. Heben Sie die Klemme mit der Elektrode mehrmals an und senken Sie sie wieder ab, um sicherzustellen, dass sie sich fließend bewegt und dass die Elektrode parallel zum Tisch liegt.





- INITIAL POWER
- BETRIEBSLEISTUNG
- VERZÖGERUNGSZEIT
- SCHWEISSZEIT
- ABKÜHLZEIT.
Wenn eine neue Art von Material getestet wird, wird dringend empfohlen, die Parameter der Schweißzyklen mit niedrigen Werten in das System einzugeben und dann ihre Werte schrittweise zu erhöhen, bis der wünschenswerteste Schweißeffekt erreicht ist.
14. Stellen Sie die Höhe der Elektrodenpressung, die für den Schweißprozess verwendet wird, mit Hilfe des manuell betätigten Druckminderers ein (Abb. 8 - Ziffer 7).
15. Drücken Sie auf dem HMI-Bedienfeld: HMI → Hauptbildschirm → Aktueller Modus → 0 oder 1
16. Drücken Sie auf dem HMI-Bedienfeld: HMI → Hauptbildschirm → Kondensatorregelung →
Der Strommodus 0/1 und die Kondensatorregelung 0 / 1 sind im Kapitel 6.5.4 ausführlich beschrieben.
17. Stellen Sie den Wert für die Leistungskorrektur ein, wenn er benötigt wird. Dieser Parameter wird in Kapitel 6.5.4 beschrieben.
18. Vergewissern Sie sich, dass eine Isolierunterlage auf dem Arbeitstisch oder auf der Trennwand aus Aluminiumblech sauber ist - sie darf an der Stelle, an der die Elektrode gegen das geschweißte Material gedrückt wird, weder verschmutzt noch mechanisch beschädigt sein.
ACHTUNG! Die Isolierplatte muss direkt unter dem zu schweißenden Material angebracht werden, da sie den Bediener vor einem Lichtbogen zwischen der Schweißelektrode und dem Arbeitstisch schützen soll.
ACHTUNG! Wenn die Trennwand mit der Isolierunterlage überzogen wurde, sollte sie fest auf dem Tisch haften - so, dass keine Verunreinigungen zwischen Trennwand und Arbeitstisch zu finden sind.
Achtung! Vermeiden Sie es, etwas unter die Masseelektrode zu legen. Wenn es während des Schweißvorgangs erforderlich ist, das zu schweißende Material unter die Masseelektrode zu legen, sollte die Schicht unter der Masseelektrode so dünn wie möglich sein.
19. Senken Sie die Klemme mit der Elektrode mit Hilfe des Fußhebels ab. Beobachten Sie, ob die Meldung erscheint im Hauptfenster des HMI-Bedienfelds und informiert darüber, dass die Elektrode die untere Position erreicht hat.
20. Drücken Sie beide START-Tasten gleichzeitig, wenn die Elektrode auf das Material gedrückt wird. Halten Sie die START-Tasten gedrückt, bis die im Rezept eingestellten Schweißparameter heruntergezählt sind. Wenn Sie die Tasten während des Zyklus loslassen, wird der Zyklus gestoppt.
ACHTUNG! Um die Hochfrequenzschweißung einzuschalten, müssen beide START-Tasten an den Steuerständen gleichzeitig gedrückt werden. Benutzen Sie beide Hände für diesen Vorgang. Im Handbetrieb müssen Sie die Tasten drücken und dürfen sie während der gesamten Schweißzeit nicht loslassen. Alle anderen Handlungen, bei denen die Tasten nicht mit beiden Händen gedrückt werden, sind strengstens untersagt.
ACHTUNG: Der Schweißvorgang in der Maschine wird an der Signalleuchtsäule (orangefarbenes Licht) angezeigt.
ACHTUNG: Während des Schweißens ist es strengstens verboten, sich der Zange, der Elektrode oder dem Wellenleiter zu nähern, geschweige denn sie mit Körperteilen oder Metallgegenständen zu berühren, da die Gefahr von Verbrennungen, Lichtbogenentzündungen oder Werkzeugverschmutzung besteht.
ACHTUNG: Die NOT-AUS-Taste ist so konzipiert, dass sie jederzeit betätigt werden kann, insbesondere wenn die Notabschaltung sofort erforderlich ist.
21. Beobachten Sie die Anzeigen auf dem Amperemeter. ANODENSTROM - Der Plattenstrom sollte im Bereich des grünen Bereichs ansteigen, der auf der Tabelle des Amperemeters angegeben ist.
22. Ziehen Sie die Elektrode mit dem Fußhebel hoch und prüfen Sie die Qualität der Schweißnaht.
23. Überprüfen Sie die Glattheit der Schweißnaht.
24. Je nach Ergebnis der ersten Schweißung (geschweißt, nicht geschweißt, überhitzt) die Schweißparameter entsprechend anpassen:
- INITIAL POWER
- BETRIEBSLEISTUNG
- VERZÖGERUNGSZEIT
- SCHWEISSZEIT
- ABKÜHLZEIT
- DRUCK (manuell einstellen)
- POWER LEVEL (manuell einstellen)
- AKTUELLER MODUS
- KONDENSATORREGELUNG
- LEISTUNGSKORREKTUR.
25. Die Maschine sollte viele Teststunden durchlaufen. Sie sollte getestet werden, wenn das Produkt wiederholbar ist. Es wird dringend empfohlen, den Arbeitszyklus der Maschine, ihre Funktionalität und Ergonomie in der Produktionslinie zu prüfen.
26. Nach Erhalt eines zufriedenstellenden Schweißergebnisses hinsichtlich der Festigkeit und der optischen Ästhetik schreiben Sie die Schweißparameter als Rezept: HMI → Hauptbildschirm → Schaltfläche Rezept speichern → Fenster Rezeptdatenbank → in der Spalte NAME den neuen Namen des Rezepts eingeben→ Schaltfläche auswählen
. Das neue Rezept erscheint in der Rezeptliste.
6.9 Einschaltdauer und Pflichten des Bedieners

1. Booten Sie das Gerät gemäß dem in Kapitel 6.7 beschriebenen Verfahren.



- Anfangsleistung;
- Betriebsleistung;
- Verzögerungszeit;
- Zeit zum Schweißen;
- Abkühlungszeit
- Leistungsstufe




ACHTUNG: , Der HF-Vorgang kann jederzeit mit der Taste STOP an der Kontrollstation gestoppt werden.
ACHTUNG: Zum Einschalten der HF-Schweißanlage müssen beide START-Tasten an den Steuerständen gleichzeitig gedrückt werden. Verwenden Sie beide Hände für diesen Vorgang. Im Automatikbetrieb ist es nicht notwendig, die Tasten für die gesamte Dauer des Zyklus gedrückt zu halten. Im automatischen Zyklus werden die Tasten nur zum Starten des Schweißvorgangs verwendet. Alle anderen Handlungen, bei denen die Tasten nicht mit beiden Händen gedrückt werden, sind strengstens untersagt.
ACHTUNG: Der Schweißvorgang in der Maschine wird an der Signalleuchtsäule (orangefarbenes Licht) angezeigt.
ACHTUNG: Während des Schweißens ist es strengstens verboten, die Zange, die Elektrode oder den Wellenleiter mit Körperteilen oder Metallgegenständen zu berühren, da die Gefahr von Verbrennungen, Lichtbogenentzündungen oder der Zerstörung von Werkzeugen besteht.

Neben der Ausgangsleistung, der Anpresskraft und der parallelen Anordnung der Elektroden ist auch die Art des Trägermaterials, das auf die geerdete Rolle unter der Folie aufgetragen wird, von großer Bedeutung für den Schweißprozess. Vermeiden Sie das Schweißen ohne eine Schicht Basismaterial - die Verwendung von Basismaterial verringert das Risiko von elektrischen Schlägen. Das Trägermaterial sollte einen geringen dielektrischen Verlust aufweisen. Dies können z. B. Epoxid-Glasplatten, Polytetrafluorethylen (Teflon), Polyester (MYLAR), Presspanplatten, Resotex, Bakelit usw. sein. Dicke und Härte des Trägermaterials hängen von der Dicke der geschweißten Folie ab. In der Regel sollte dünneres Trägermaterial für dickere Folien und dickeres Trägermaterial - für dünnere Folien verwendet werden. Die Dicke des Trägermaterials kann zwischen 0,1 und 1,5 [mm] liegen und sollte für den jeweiligen Folientyp und die Schweißbedingungen in mehreren Versuchen ausgewählt werden.
ACHTUNG: Das Schweißen ohne Grundierung sollte vermieden werden. Die Verwendung einer geeigneten Unterlage reduziert die Anzahl der Überspannungen an der Elektrode.
7.2. AUSWAHL DER AUSGANGSLEISTUNG
Um die höchstmögliche Leistung und eine geringe Anzahl von Ausschuss zu erreichen, stellen Sie die Leistung für jede Elektrode mit dem POWER LEVEL-Schalter ein. Das erste Element ermöglicht die Einstellung der Stromversorgung des Generators, während das zweite Element die Einstellung der Leistung ermöglicht, die der Elektrode zugeführt und an das geschweißte Material abgegeben wird. Die Einstellung der Leistung sollte im Laufe mehrerer Versuche erfolgen (gemäß den Anweisungen des Herstellers).
Wenn Sie die Ausgangsleistung erhöhen, beobachten Sie das Amperemeter, das den Anodenstrom misst. Wenn der Strom ansteigt, bedeutet dies, dass der Schweißvorgang eingeleitet wird.
Die Schweißzeit sollte so eingestellt werden, dass die Hochfrequenz abgeschaltet wird, wenn der Zeiger des Amperemeters stehen bleibt. Prüfen Sie die Qualität der Schweißung. Wenn die Qualität unzureichend ist, erhöhen Sie die Ausgangsleistung, und wenn dies nicht hilft, erhöhen Sie die Schweißzeit. Stellen Sie keine zu hohe Ausgangsleistung ein - dies kann zu einer Beschädigung der Produkte oder sogar des Grundmaterials und der Elektroden führen.
In der Regel ist davon auszugehen, dass beim Schweißen von Hart-PVC die Schweißzeit 4 - 5 Sekunden nicht überschreiten sollte. Die Versuche haben gezeigt, dass eine längere Schweißzeit, die über den oben genannten Bereich hinausgeht, praktisch keine Auswirkungen auf die Schweißqualität hat, aber die Effizienz des Prozesses deutlich verringert. Wenn die von Ihnen durchgeführten Experimente zeigen, dass der Schweißvorgang länger als acht Sekunden dauert, deutet dies nur auf eine ungeeignete Wahl des Generators für die Last oder die Installation einer Elektrode mit zu großer Oberfläche hin. Nachdem die Spannung von den Elektroden abgeschaltet wurde, sollten die geschweißten Materialien unter der Pressvorrichtung abkühlen. Wird die Elektrode zu früh abgehoben, wenn das Material noch formbar ist, wird das geschweißte Material unangemessen abgekühlt und verformt sich. Der positive Einfluss der Elektrode auf den Abkühlungsprozess ist leicht zu verstehen, wenn man sich vergegenwärtigt, dass die Elektrode zwar sehr warm zu sein scheint, ihre Temperatur aber immer noch viel niedriger ist als die Temperatur der geschweißten Folie. Daher kann die Elektrode die Wärme der geschweißten Folie aufnehmen und sie schnell abkühlen.
Daher ist es notwendig, das geschweißte Material 0,52 Sekunden lang unter dem Pressgerät abkühlen zu lassen. Die Abkühlzeit sollte in mehreren Versuchen ermittelt werden, wobei zu beachten ist, dass eine zu lange Abkühlzeit unnötige Verluste an Produktionszeit bedeutet.
Das Schweißen von Weich-PVC-Folie erfordert einen Druck der Elektroden auf das zu verschweißende Material. Die Messung des optimalen Elektrodendrucks könnte sich als schwierig erweisen und ist in der Praxis nicht wirklich notwendig. Um den richtigen Druck einzustellen, reicht es in der Regel aus, Fälle von fehlerhaftem Schweißen und das Aussehen von fehlerhaftem Schweißen zu erkennen, die auf eine falsche Einstellung des Drucks hinweisen könnten. Ein zu niedriger Druck kann durch die folgenden Symptome angezeigt werden:
- Anfälligkeit für Funkenentladungen zwischen zwei Elektroden, da sich die Luft, die eigentlich herausgedrückt werden sollte, zwischen zwei Folienschichten befindet und sich dadurch eine ungleichmäßige Stromstärke bildet;
- Auftreten von Luftblasen in der Naht;
- das Erscheinungsbild der Nahtstärke, die gering ist
Wenn der Druck besonders niedrig ist, kann es zum so genannten "Filmsieden" kommen. Wenn die Folie unter sehr niedrigem Druck geschweißt wird, kann sie sich zu einem schaumigen Produkt mit sehr geringem Widerstand verformen. Ein zu hoher Druck ist ebenfalls ungeeignet, da er die Folie an der Schweißstelle sehr dünn werden lässt und somit zu einem geringeren Widerstand des geschweißten Materials führen kann. Daher wird empfohlen, den Grundsatz zu befolgen, dass die Dicke der Folie nach dem Schweißen mindestens die Hälfte der ursprünglichen Dicke der beiden Folienschichten betragen sollte. Das Auftreten und die richtige Form der charakteristischen Leckage, die sich in der Regel an beiden Rändern der geschweißten Stelle bildet, hat ebenfalls einen erheblichen Einfluss auf die Widerstandseigenschaften des geschweißten Materials. Wenn eine solche Leckage nicht auftritt, deutet dies in der Regel auf eine unzureichende Widerstandsfähigkeit der geschweißten Stelle hin, die sehr leicht geprüft werden kann. Das Ausbleiben der Leckage nach dem Schweißvorgang kann auf eine zu geringe Ausgangsleistung oder einen zu geringen Druck zurückzuführen sein. Wenn Sie Elektroden mit Schneidkanten verwenden, ist es sehr wichtig, die Schneidkante richtig zu positionieren. In der Regel wird davon ausgegangen, dass die Schneide der Elektrode etwa um die Hälfte der Dicke der geschweißten Folie aus der Schweißebene herausragen sollte. Um die Funktion der Schneide zu überprüfen, müssen mehrere Testschweißungen durchgeführt und die Folienreste entfernt werden. Das Ergebnis der Tests kann als zufriedenstellend angesehen werden, wenn das Entfernen der Folienreste entlang der Schweißlinie nicht mehr als einen Schnitt mit einer Schere erfordert.
8.0 Wartung
Dank der angewandten Konstruktionslösungen und des unkomplizierten Aufbaus der Maschine sind sowohl die vorbeugenden als auch die Notfall-Wartungs- und Kontrolltätigkeiten relativ einfach und erfordern keine langen Betriebspausen der Maschine.
Die Schweißmaschine erfordert einen geringen Arbeitsaufwand im Zusammenhang mit dem Betrieb und der Wartung der Maschine, vorausgesetzt, dass die entsprechenden Betriebsbedingungen eingehalten werden. Es ist notwendig, den technischen Zustand des Maschinenanschlusses an das Stromnetz regelmäßig zu überprüfen, insbesondere den Zustand des Stromschlagschutzsystems.
Alle Bauteile des Hochfrequenzgenerators, insbesondere alle Isolierelemente, müssen sauber gehalten werden. Das Innere des Ausgangssystems des Generators sollte mindestens einmal alle drei Monate gründlich gereinigt werden. Bei dieser Reinigung ist der Zustand der Komponenten des Generators und der Geräte, die direkt mit dem Generator zusammenarbeiten, zu überprüfen und alle Verbindungen sind nachzuziehen.
Aufgrund der spezifischen Eigenschaften der Maschine wird empfohlen, einige der oben genannten Arbeiten von autorisiertem und entsprechend qualifiziertem technischem Servicepersonal des Herstellers durchführen zu lassen (dies gilt insbesondere für Notfälle). Die vorgenannten Arbeiten erfordern besondere Sorgfalt und Aufmerksamkeit.
ACHTUNG! Während des Betriebs des Generators haben seine Komponenten sowie die Komponenten des Ausgangskreises eine Spannung von bis zu 8 kV DC und eine Hochfrequenzspannung von bis zu 220 V (27,12 MHz).
ACHTUNG: Die Kondensatoren des Anodengenerators können eine elektrische Ladung mit einer Spannung von bis zu 8000 VDC halten, auch nachdem die Schweißmaschine von der Stromversorgung getrennt wurde. Vor dem Berühren der Komponenten des Hochfrequenzgenerators müssen diese Kondensatoren immer entladen werden.
Die Erdung der Maschinenstruktur muss mit besonderer Sorgfalt vorgenommen werden. Denken Sie daran, dass der Generator niemals in Betrieb genommen werden darf, wenn die Schutzvorrichtungen entfernt sind, auch nicht bei technischen Service- und Wartungsarbeiten, wenn das Sicherheitsniveau der Maschine aufgrund der durchgeführten Reparaturen niedriger sein kann.
Alle Wartungsarbeiten und Reparaturen bedürfen einer Genehmigung der autorisierten Personen.
Sie sollten ein MASCHINENPROTOKOLLführen, in dem die Daten und Arten der durchgeführten Präventivmaßnahmen oder Reparaturen festgehalten werden.
Betreten Sie während der Wartungsarbeiten oder anderer erforderlicher manueller Tätigkeiten niemals den Bereich, der potenziellen und vorhersehbaren Gefahren ausgesetzt ist, und bringen Sie keine Körperteile dorthin, um das Risiko potenzieller und vorhersehbarer Gefahrensituationen auszuschließen.
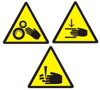
Tragen Sie immer Schutzkleidung und rutschfeste Schuhe, um das Risiko eines Sturzes zu verringern. Achten Sie immer darauf, dass Ihre Ärmel gut um die Handgelenke geschlungen oder richtig hochgekrempelt sind.
Tragen Sie immer Arbeitshandschuhe, wenn Sie mit scharfkantigen Bauteilen arbeiten.
Das gesamte Personal, das für die Bedienung und Wartung der Maschine verantwortlich ist, sollte entsprechend geschult und unterwiesen werden.
Alle Wartungs- und Reparaturarbeiten dürfen nur von autorisiertem und qualifiziertem Personal durchgeführt werden, das in der Lage ist, Mängel und Fehler richtig zu interpretieren, Installationspläne und technische Zeichnungen zu lesen, um sicherzustellen, dass alle Demontage- und Montagearbeiten im Zusammenhang mit den Standard-Wartungsverfahren professionell und vor allem sicher durchgeführt werden.
Alle Arbeiten im Bereich des Betriebs der Presseinheit, d. h. Montage und Demontage der Elektrode, die bei eingeschalteter Stromversorgung der Maschine durchgeführt werden, dürfen ausschließlich von Personal ausgeführt werden, das in Bezug auf den Arbeitsschutz und insbesondere auf die mit dem Betrieb der Presseinheit verbundenen Risiken entsprechend geschult ist.
Sie sollten auch das mögliche abweichende Verhalten der Maschine vorhersehen, wenn das pneumatische System der Schweißmaschine oder die Druckluftzufuhrkanäle nicht abgedichtet sind. Dies führt zu einem langsamen automatischen Absenken der Presseinheit der Schweißmaschine.
Das Personal sollte im Rahmen der Schulung zum Thema Arbeitsschutz über dieses Risiko informiert werden.
ACHTUNG: Bei jedem der oben genannten Vorgänge muss der Betrieb der Maschine gestoppt werden.
8.2 Präventivprogramm - Regelmäßige Kontrollen
ZU BEGINN EINER JEDEN SCHICHT
- Prüfen Sie, ob der Arbeitsbereich der Maschine sauber und aufgeräumt ist;
- Prüfen Sie visuell, ob die Schutzschirme gesperrt sind;
- Kontrollieren Sie die Beleuchtung des Arbeitsbereichs;
- Prüfen Sie, ob die NOT-AUS-Taste richtig funktioniert;
- Überprüfen Sie den Hauptschutz in der Elektroinstallation;
- Überprüfen Sie den Zustand der leitenden Elemente aus Kupfer und Messing im Bereich des Elektrodenhalters und der Erdungselemente der Seitenschutzgitter.
ALLE 100 BETRIEBSSTUNDEN DER MASCHINE (MINDESTENS EINMAL PRO WOCHE):
- Prüfen Sie, ob die tragenden Schrauben (insbesondere auch die Schrauben zur Befestigung der Werkzeuge) richtig befestigt und angezogen sind;
- Prüfen Sie den Kondenswasserstand im Druckluftfilterbehälter; wenn Wasser vorhanden ist, leeren Sie den Behälter; wenn große Mengen fester Verunreinigungen vorhanden sind, zerlegen Sie den Behälter und waschen Sie ihn;
ALLE 500 BETRIEBSSTUNDEN DER MASCHINE (MINDESTENS JEDOCH ALLE ZWEI WOCHEN)
- Prüfen Sie, ob der Strahler der Anodenlampe sauber ist;
- Überprüfen Sie die Menge an festen Verunreinigungen und Staub in der Generatorkammer; falls nötig, reinigen Sie die Kammer mit einem Staubsauger oder einer Druckluftpistole;
- Prüfen Sie, ob die beweglichen Elemente (insbesondere die Werkzeuge und Führungen) sauber sind;
- Schmieren Sie die beweglichen Elemente - insbesondere die Führungen; wenn nötig, verwenden Sie ein festes Schmierfett auf Lithiumbasis und eine Fettpresse;
- Prüfen und testen Sie die Alarmanlage.
ALLE 1000 BETRIEBSSTUNDEN DER MASCHINE (MINDESTENS JEDOCH ALLE SECHS MONATE)
- Kontrollieren Sie visuell den Zustand der mechanischen Elemente;
- Ziehen Sie alle Schrauben fest;
- Prüfen Sie, ob die Schutzmaßnahmen gegen Stromschlag ordnungsgemäß funktionieren;
- Überprüfen Sie die Wirksamkeit der Schmierung der Führungen;
- Überprüfen Sie den Zustand der Hauptkontaktelemente - Hauptschütze oder andere Kontaktelemente des Systems, wie Schütze oder Relais mit übermäßig abgenutzten Oberflächen müssen ersetzt werden.
ACHTUNG: Vor jeder Wartung die Maschine mit dem HAUPTSCHALTER ausschalten und den Netzstrom abschalten.
ACHTUNG: Vor jeder Wartung die Maschine mit dem HAUPTSCHALTER ausschalten und den Netzstrom abschalten.
Die wichtigsten Elemente, die in der Maschine verwendet werden, um die Sicherheit des Betriebs zu erhöhen und zu gewährleisten, sind:
- Detektoren mit offenem Gehäuse
- leicht zugänglicher NOT-AUS-Schalter auf dem Steuerschalter, der die Maschine jederzeit ausschaltet
- eine Reihe von Sensoren und Detektoren, die das ordnungsgemäße Funktionieren der Maschine und ihrer einzelnen Systeme kontrollieren und mit der Signalisierung auf dem Bedienpult verbunden sind
- zusätzliche Sicherheitsvorkehrungen im Algorithmus der Maschinensteuerung, die verhindern, dass die Maschine in potenziell gefährlichen Situationen anläuft
- Die Struktur der Maschine selbst gewährleistet ein Höchstmaß an Betriebssicherheit.
9.1 Grundlegende Anforderungen
Die Themen Arbeitsschutz und Risikobeurteilung beim Kontakt einer Person mit der Maschine wurden in den vorangegangenen Kapiteln dieses Handbuchs ausführlich beschrieben. Da dieses Thema äußerst wichtig ist, werden einige Anweisungen in diesem Abschnitt wiederholt.- Die Maschine darf ausschließlich in einer Art und Weise verwendet werden, die ihrem in Punkt 1 ausdrücklich beschriebenen Zweck entspricht.
- Die angewandten Konstruktionslösungen in Bezug auf die Sicherheit reduzieren sowohl das nicht normgerechte Verhalten der Maschine als auch die Gefahren für die Bediener und andere Personen, die mit der Maschine in Berührung kommen, auf ein Minimum, vorausgesetzt, die Grundsätze der sicheren Arbeit werden eingehalten. Die Maschine ist mit Schlüsselschaltern auf Schutzschirmen und einer NOT-AUS-Taste ausgestattet.
- Jeder neue Mitarbeiter, der mit der Schweißmaschine in Berührung kommt, sollte in den Grundprinzipien des Arbeitsschutzes geschult und mit den Gefahren beim Betrieb der Schweißmaschine vertraut gemacht werden, es sei denn, der Bediener hält sich an die vorgeschriebenen Vorschriften und Grundsätze.
- Das mit der Bedienung der Schweißmaschine beauftragte Personal muss über gründliche Kenntnisse in Erster Hilfe bei Stromschlägen und Verbrennungen verfügen. Bei Personen, die mit Geräten arbeiten, die elektromagnetische Wellen im Frequenzbereich von 0,1 - 300 MHz verwenden, sind regelmäßige ärztliche Untersuchungen erforderlich.
- Nach der Installation der Schweißmaschine muss die Emission des elektromagnetischen Feldes gemessen und die Grenzen des Gefahrenbereichs festgelegt werden.
- ACHTUNG: Die Lampe enthält Seltenerdmetalle und Seltenerdmetalloxide, die hochgiftig sind. Im Falle eines Bruchs muss die Lampe mit äußerster Sorgfalt und mit Hilfe von spezialisierten Diensten entsorgt werden
- Auf der Grundlage der Messergebnisse werden der Gefährdungsgrad und die Zeit, in der sich das Personal im Gefahrenbereich aufhalten darf, gemäß den geltenden Normen festgelegt.
- Nur Bediener, die auf der Grundlage spezieller medizinischer Untersuchungen über eine entsprechende Zulassung für die Arbeit im Bereich elektromagnetischer Felder verfügen und ordnungsgemäß in der sicheren Bedienung der Geräte, die elektromagnetische Felder ausstrahlen, geschult wurden, dürfen den Gefahrenbereich betreten.
- Die vorgenannten Messungen sollten von einer autorisierten Institution durchgeführt werden. Detaillierte Anweisungen zu solchen Messungen sind in den geltenden Vorschriften des Landes, in dem die Maschine verwendet wird, festgelegt.
- Der Empfänger des Gerätes trägt die volle rechtliche und finanzielle Verantwortung für alle Ereignisse, die aus der Unkenntnis dieser Dokumentation oder der Nichtbeachtung der Sicherheitsvorschriften resultieren. Das Lesen und Befolgen ihrer Kennzeichnung ist UNBEDINGT MUSS
- Der Lieferungsempfänger ist verpflichtet, auf der Grundlage der in dieser Dokumentation enthaltenen Informationen und der Kenntnis seiner eigenen Produkttechnologie ein Arbeitshandbuch für die Mitarbeiter, die diese Maschine bedienen, zu erstellen.
- Jeder Bediener muss sich vor Beginn der Arbeiten an der Maschine mit dem Inhalt dieser Dokumentation vertraut machen und ein STATIONSHANDBUCH erstellen lassen.
- Die Maschinenbediener sollten stets normale Arbeitskleidung, Handschuhe, Kopfbedeckungen und rutschfestes Schuhwerk tragen.
- Die Arbeitsumgebung der Maschine, der Boden und die Handgriffe müssen stets sauber und frei von Verunreinigungen, Fett oder Schlamm sein, um das Risiko eines Ausrutschens oder Sturzes so gering wie möglich zu halten.
- Benutzen Sie die Maschine niemals im Automatikbetrieb ohne die feststehenden oder beweglichen Schutzelemente. Prüfen Sie regelmäßig, ob alle Notschalter und alle anderen Schutzelemente richtig montiert sind und einwandfrei funktionieren.
- Jeder Bediener der Maschine muss über die Funktionen der Schutzelemente der Maschine und deren ordnungsgemäße Verwendung unterwiesen werden.
- In der Umgebung der Maschine (ca. 1,5 m um die Maschine herum) dürfen sich keine Gegenstände befinden, die den Betrieb der Maschine beeinträchtigen könnten. Dieser Bereich muss sauber gehalten werden und über eine angemessene Beleuchtung verfügen.
- Verwenden Sie niemals die Manipulatoren der Maschine oder flexible Rohre als Halterung. Denken Sie daran, dass jede versehentliche Bewegung des Manipulators der Maschine den Betrieb der Maschine versehentlich in Gang setzen kann.
- Informieren Sie immer den Vorgesetzten und/oder das Verkehrspersonal über alle Fälle von Fehlbedienung der Maschine.
- Alle Wartungsarbeiten und Reparaturen bedürfen einer Genehmigung der autorisierten Personen.
- Sie sollten ein Maschinenprotokollmit den Daten und Arten der durchgeführten Präventivmaßnahmen oder Reparaturen.
- Betreten Sie während der Wartungsarbeiten oder anderer erforderlicher manueller Tätigkeiten niemals den Bereich, der potenziellen und vorhersehbaren Gefahren ausgesetzt ist, und bringen Sie keine Körperteile dorthin, um das Risiko potenzieller und vorhersehbarer Gefahrensituationen auszuschließen.
VERWENDEN SIE DIE SCHWEISSMASCHINE NIEMALS, WENN DIE SCHUTZVORRICHTUNGEN ENTFERNT ODER DIE SCHLÜSSELSCHALTER BLOCKIERT SIND. DIES GILT INSBESONDERE FÜR DIE SCHUTZSCHIRME DES GENERATORS. Diese Schutzschirme reduzieren die Emission von elektromagnetischen Feldern und verhindern ein versehentliches Berühren der Elemente des Stromkreises mit Versorgungsspannung oder Hochspannung bis 8000 V.
- Tragen Sie immer Schutzkleidung und rutschfeste Schuhe, um das Risiko eines Sturzes zu verringern. Achten Sie immer darauf, dass Ihre Ärmel gut um die Handgelenke geschlungen oder richtig hochgekrempelt sind.
- Tragen Sie immer Arbeitshandschuhe, wenn Sie mit heißen oder scharfkantigen Bauteilen arbeiten.
- Es ist auch zu beachten, dass an den Bauteilen, die aus ergonomischen Gründen nicht abgeschirmt sind, also an der Elektrode und den leitenden Teilen des Elektrodenhalters, Hochfrequenzspannung anliegt. BERÜHREN SIE DIESE TEILE NIEMALS WÄHREND DES SCHWEISSENS.
- Die Berührung dieser Bauteile während des Schweißvorgangs führt zu einer Verbrennung der Haut durch Hochfrequenzspannung. Es besteht jedoch keine Gefahr für Leben und Gesundheit.
- Die gewählte Art der Stromversorgung der Schweißmaschine birgt ein potentielles Risiko von Quetschungen von Gliedmaßen im Raum zwischen den Pressungen der Elektroden. Alle Arbeiten im Arbeitsbereich des Pressgerätes, d.h. Montage und Demontage von Elektroden oder das Verteilen und Entfernen von Material und Schrott, die bei angeschlossener Schweißmaschine durchgeführt werden, dürfen ausschließlich von Mitarbeitern durchgeführt werden, die auf dem Gebiet des Arbeitsschutzes geschult sind, einschließlich der Information über die vom Pressgerät ausgehende Gefahr.
- Während des Betriebs der Maschine sollte sich der Bediener in dem unten dargestellten Bereich aufhalten
ZD-NX-4 Arbeitsbereich (grüne Farbe)
9.3 Bedingungen für die Arbeitssicherheit des Personals, das für die Wartung und Instandhaltung der Schweißmaschine zuständig ist- Alle Wartungsarbeiten und Reparaturen bedürfen einer Genehmigung der autorisierten Personen.
- Es ist VERBOTEN, Wartungs-, Instandhaltungs- oder Präventivarbeiten durchzuführen, ohne die Maschine von der Stromversorgung zu trennen. Diese Arbeiten erfordern besondere Sorgfalt. Es muss immer daran gedacht werden, dass die Kondensatoren des Anodengenerators eine elektrische Ladung mit einer Spannung von 5000 V halten können, auch nachdem die Schweißmaschine vom Stromnetz getrennt wurde. Vor dem Berühren der Komponenten des Hochfrequenzgenerators müssen diese Kondensatoren immer entladen werden.
- Es ist VERBOTEN, die Maschine während des Betriebs zu schmieren.
- Das gesamte Personal, das für die Bedienung und Wartung der Maschine verantwortlich ist, sollte entsprechend geschult und unterwiesen werden.
- Während des Betriebs des Generators stehen seine Komponenten sowie die Komponenten des Ausgangskreises unter Hochfrequenzspannung. Die Erdung der Maschinenstruktur muss mit besonderer Sorgfalt durchgeführt werden. Es ist auch zu beachten, dass die Betriebszeit des Generators mit abgenommenen Schutzschilden auf ein Minimum reduziert werden muss.
- Alle Reparaturen müssen in Übereinstimmung mit den geltenden Grundsätzen für die Reparatur und den Betrieb von Geräten von einer Person durchgeführt werden, die über ein entsprechendes Zertifikat verfügt, das von der zuständigen Elektrikervereinigung (in Polen: SEP) ausgestellt wurde.
- Alle Wartungs- und Reparaturarbeiten dürfen ausschließlich von autorisiertem und qualifiziertem Personal durchgeführt werden, das in der Lage ist, Mängel und Fehler richtig zu interpretieren und Installationspläne zu lesen, um sicherzustellen, dass alle Demontage- und Montagearbeiten im Zusammenhang mit den Standardwartungsverfahren professionell und vor allem sicher durchgeführt werden.
- Betreten Sie während der Wartungsarbeiten oder anderer erforderlicher manueller Tätigkeiten niemals den Bereich, der potenziellen und vorhersehbaren Gefahren ausgesetzt ist, und bringen Sie keine Körperteile dorthin, um das Risiko potenzieller und vorhersehbarer Gefahrensituationen auszuschließen.
- Verwendung der Maschine auf andere Weise als in dieser Betriebs- und Wartungsanleitung beschrieben
- unsachgemäße Installation, die nicht in Übereinstimmung mit den in diesem Handbuch beschriebenen Verfahren durchgeführt wurde
- unsachgemäße Bedienung der Maschine oder deren Bedienung durch nicht entsprechend geschultes Personal
- maschinelle Versorgung mit ungeeigneten Parametern
- unzureichende Wartung der Maschine
- unbefugte Änderungen oder Eingriffe durch Personen ohne die erforderlichen Lizenzen, Genehmigungen oder Schulungen,
- Verwendung von Ersatzteilen, die nicht Originalteile sind
- Handlungen von Personen, die nicht in Übereinstimmung mit den in dieser Betriebs- und Wartungsanleitung aufgeführten Grundsätzen und Warnhinweisen stehen.
10.0 Elektrische Dokumentation
10.1 Stromversorgungsparameter - Technische Daten
Stromversorgung |
3 x 220 VAC; 50/60 Hz |
Kopfschutz |
40 A |
Installierte Kapazität |
6 kVA |
HF-Ausgangsleistung |
4 kW |
Betriebsspannung |
24 VDC |
Betriebsfrequenz |
27,12 MHz |
Frequenzstabilität |
+/- 0.6 % |
Generatorlampe (Metall-Keramik-Triode) |
7T85RB |
Anti-Entladungs-Kreislaufsystem |
ANTIFLASH komplett mit HF-Filter |
10.2 Liste der elektrischen Geräte
Alle in der Maschine verwendeten Komponenten sind typische elektrische Bauteile, die in jedem Fachgeschäft erhältlich sind. Der Hersteller überlässt bei der Auswahl dieser Bauteile im Falle ihres Austauschs dem Empfänger die Wahl, vorausgesetzt, dass die verwendeten Ersatzbauteile die gleichen technischen Parameter aufweisen. Die Liste der elektrischen Geräte ist in Kapitel 13.3 enthalten. Wenn Sie Fragen haben, wenden Sie sich bitte an den Hersteller.
10.3 Konzeptzeichnungen für die Elektroinstallation
HINWEIS: Der Schaltplan befindet sich im Anhang zu dieser Anleitung.
Siehe Anhang
11.0 Pneumatische Dokumentation
11.1 Technische Daten
Betriebsdruck |
0,4 - 0,8 MPa |
Druckluftverbrauch |
Max. 11 nl (Standard) pro Zyklus |
Reinheit der Luft |
gemäß ISO8573-1:4-4-4 |
Leistung der Filterung |
20 um (ISO8573-1 4-4-4) |
Das pneumatische System der Schweißmaschine erfüllt seine Funktion:
- Presseeinheit

SEHEN ANHÄNGE
12.0 Allgemeine Anweisungen
12.1 Allgemeine Anweisungen
Die angewandten Konstruktionslösungen und die hochwertigen Komponenten ermöglichen einen ordnungsgemäßen Betrieb der Maschine für einen Zeitraum von etwa 30 Jahren. Es können jedoch Änderungen in den Bedürfnissen des Endnutzers oder Änderungen in den Grundsätzen oder Normen auftreten, die heute noch nicht vorhersehbar sind und eine Entsorgung der Maschine vor Ablauf des genannten Zeitraums erforderlich machen können. Dies gilt auch für ausgetauschte oder reparierte Teile oder Komponenten der Schweißmaschine.
Der Endnutzer ist verpflichtet, dafür zu sorgen, dass die Entsorgung der Maschine oder ihrer Bestandteile in Übereinstimmung mit den zu einem bestimmten Zeitpunkt und an einem bestimmten Ort geltenden gesetzlichen Bestimmungen erfolgt.
Alle Bestandteile der Maschine sind recycelbar. Die Entsorgung von gefährlichen Abfällen muss immer von spezialisierten Unternehmen durchgeführt werden.
Die Arten von Abfällen, die während des Lebenszyklus der Maschine anfallen, werden unter Punkt 12.2 beschrieben
12.2 Abfälle
Alle Abfälle, die im Rahmen von Austausch- oder technischen Servicetätigkeiten anfallen und mit Fett verunreinigt sind, können nicht zusammen mit Industrieabfällen entsorgt werden.- flüssige oder feste fetthaltige Abfälle
- nach dem Abschmieren oder der Wartung der Maschine verbleibendes Fett
- mit Substanzen getränkte Lappen oder Papiere, die zur Reinigung der Maschinenteile verwendet werden
- gebrauchte Ersatzteile der Maschine, je nach Material, aus dem sie hergestellt sind
- Generatorlampe!!!.
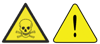
Alle Abfälle, die im Rahmen von Austausch- oder technischen Servicetätigkeiten anfallen und mit Fett verunreinigt sind, können nicht zusammen mit Industrieabfällen entsorgt werden. Alle während des Produktionsprozesses anfallenden Abfälle sind zu trennen und an ausgewiesenen und gekennzeichneten Stellen zu lagern.

12.3 Vorgehensweise bei der Demontage des Geräts vor der Entsorgung
-
- Stellen Sie die Maschine so auf, dass sie unbeweglich steht.
- Trennen Sie das Gerät von der Stromversorgung.
- Trennen Sie die Druckluftzufuhr der Maschine.
- Entfernen Sie flexible Kunststoff- oder Gummileitungen und lassen Sie sie von einem Fachunternehmen entsorgen.
- Trennen und entfernen Sie Leitungen und elektrische Geräte und lassen Sie sie von einem Fachunternehmen entsorgen.
- Trennen Sie Stahlteile und Teile aus Nichteisenmetallen und lassen Sie sie von einem Fachunternehmen entsorgen.
13.0 Anhänge
13.1 Modell- und Seriennummernschild
Jede Miller Weldmaster Maschine hat diesen Aufkleber auf der Rückseite der Maschine. Er identifiziert das Modell und die Seriennummer jedes Schweißgeräts.
Sie gibt auch die für den Betrieb erforderliche Spannung und Frequenz an.
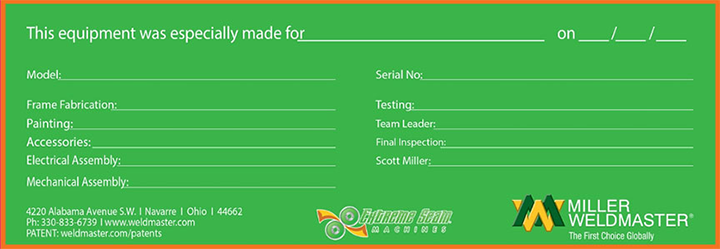